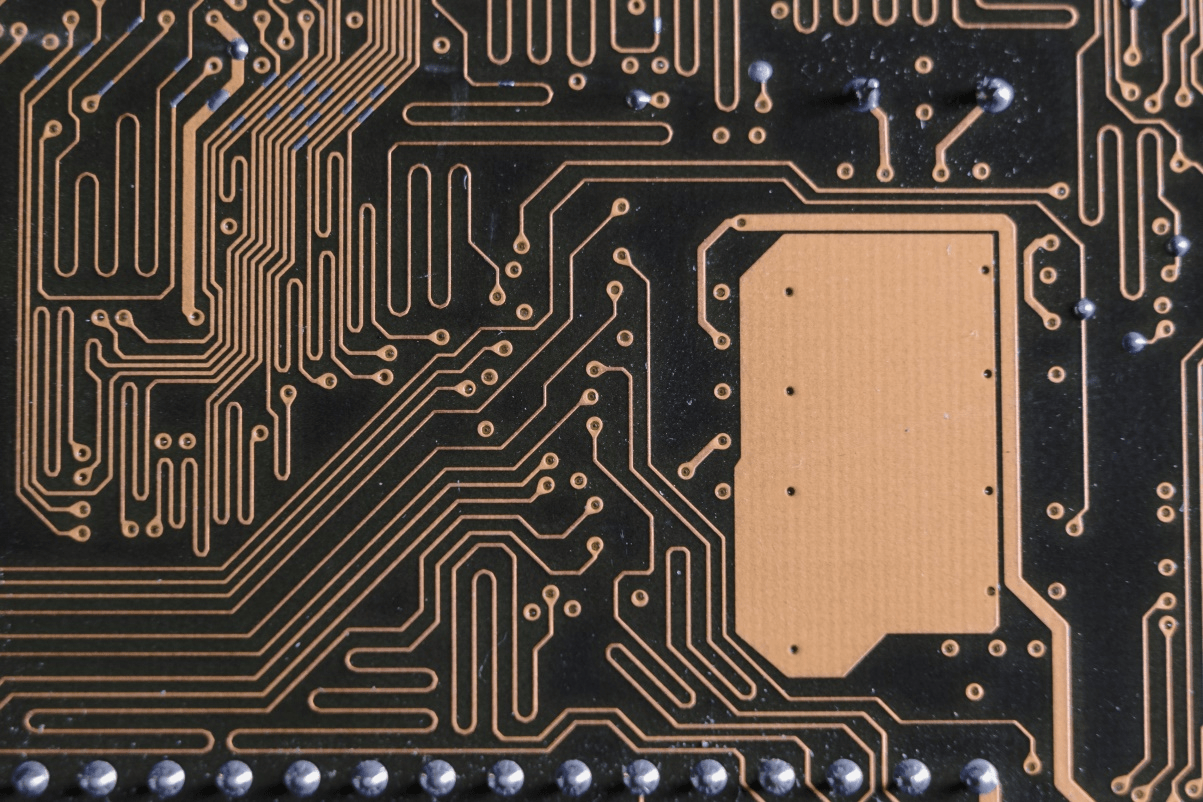
Design Guidelines and Challenges for Rigid-Flex PCB Manufacturing
Manufacturers looking to increase their production efficiency might be interested in the design guidelines for rigid-flex PCB manufacturing. Rigid-flex printed circuit boards offer several advantages over traditional rigid PCBs. However, they can also present some unique challenges that must be considered during the design phase.
During the design process of a board design, it is necessary to consider how your choices will impact the overall costs and reliability of the final product. This blog post will outline the basic principles that should be followed while designing rigid-flex PCBs.
What is a Rigid-Flex PCB Board?
The hybrid of hardboard and flexible circuits is known as a rigid-flex board. In this hybrid of hardboard and flexible circuits, manufacturing is almost identical to traditional hardboards. However, there are two types of circuitry running through a rigid-flex board. First, that can be bent or flexed (flexible) and another for consistency (rigid).
The configuration of a rigid-flex board makes it ideal for use in products with space constraints. The assembly is very much like hardboards but the materials are thin and still support weight well.
Rigid-flex boards are ideal for applications that require continuous flexing, called dynamic flex. A well-designed rigid-flex board can withstand hundreds and thousands of cycles without failure due to the flexible material. This durability is what makes it a perfect choice if you are dealing with an application with heavy use.
The different electronic devices we use today can be linked together by using flex and rigid-flex PCBs to create one single unit. With the help of these two types of boards, manufacturers can combine many separate parts into a more efficient product than before.
There are several PCB technologies, but rigid-flex PCB boards provide the most flexibility and customizability. Rigid PCBs can't contour to fit in odd spaces, nor do they allow for unique form factors like those made possible by flexible or rigid-flex PCBs.
Standard devices are shrinking, and PCBs are following suit with new advancements in technology that have allowed it to shrink its footprint while still supplying adequate voltage.
Rigid flex pcb Design Guidelines
The Rigid-Flex PCB design has two layers: a flexible layer that wraps around all parts and an insulating core. This makes it much more durable than other boards, with the flexibility to flex without breaking or cracking in extreme conditions.
The fabrication package for this type of board includes coverlayer, nomenclature, solder mask layers, and Gerber files, along with drill templates, allowing you to make your own custom designs. There are, however, some key differences in the fabrication of hardboards and rigid-flex printed circuit boards.
- The rigid-flex print should clearly define the requirements and has more dimensions to it. It should accurately define the rigid to flex transition areas as rigid-flex circuit boards are used in 3D applications.
- You and your fabricator should work out the material layup in rigid-flex printed circuit boards as it is critical. You can make the right material choices with the help of your fabricator according to your requirements. This includes mechanical considerations, UL flammability rating, impedance control on rigid and flex layers, minimum bend radii required, RoHS certifications, etc.
- To create a rigid-flex board, you need additional layers of Gerber fibers. You will require artwork in the form of coverlayer and bondply sections that define two different areas on your board - one area for copper foil tape or solder mask layer 1, while the other area is just plain hardboard. It's crucial how much material goes into this latter section as IPC 22233 recommends 0.100" thickness standard between them; more than that can be used if needed.
Rigid-Flex PCB Design Challenges
Flexible and rigid-flex PCBs come with several design challenges. However, it is worth tackling these to take advantage of all the benefits, such as durability and ease when adding or removing modules from custom designs.
In general terms, routing for both types becomes more complicated due to increased spacing requirements. You'll need wider traces (4 mil), but flexible circuitry allows bends up 90 degrees without affecting performance. This can sometimes improve efficiency while saving space on your board assembly process.
Regardless of whether your rigid-flex elements will be static, dynamic, or creased, certain considerations must be taken into account. Factors such as how much wear and tear can these parts withstand before they break down entirely? Without considering the consequences, it could mean complete failure for any project in this field.
This is a small yet important detail in the design of modern-day gadgets. With static flexible ribbons, there will be little to no movement from these components, while dynamic flex ribbons are intended to move and bend when pressure is applied which allow for more versatility. However, it is important to make sure that the flex PCB ribbon does not permanently deform during operation.
Why Choose Rigid-Flex PCB design?
Flex and rigid-flex printed circuit boards let you design electronic devices in three dimensions instead of standard PCBs, which only allow for two-dimensional designs. With this new capability comes the opportunity to create interesting form factors never seen before.
A rigid printed circuit board, contrary to its name, can break during handling or manufacturing. On the other hand, flex circuits are designed with flexibility in mind. They offer both flexibility and durability. Therefore, these types of boards are commonly used in aerospace systems and wearable electronics.
While rigid-flex printed circuit boards can cost more than rigid printed circuit boards, they offer specific features that justify their increased prices. Some of the applications of rigid-flex printed circuit boards include:
- High-density applications– Rigid-flex boards are a great way to save space on printed circuit board designs. They allow for connectors and cables that won't fit in traditional layouts due to their flexibility, which is perfect for needing an out-of-the-box solution.
- High-reliability applications– Connectors with flexible cables are unreliable when subjected to extreme vibrations and repeated or excessive shocks. For applications that must handle high vibration and the stresses of an environment that will be subject to more than one harsh cycle, rigid-flex printed circuit boards provide greater reliability.
Conclusion
Rigid-flex PCBs are a type of electronics board that combines rigid and flexible layers. Rigid-flex boards usually have 4 or more copper surfaces, which can be used for signal routing between the different layers.
To design this type of board effectively, you need to understand some basic principles while designing it. You should use a four-layer stack up with two outer planes as ground planes. You will also need to consider shielding requirements when going through the design process, so your board performs well in an RF environment.
Get a quote if you are looking for reliable rigid-flex PCB manufacturing.