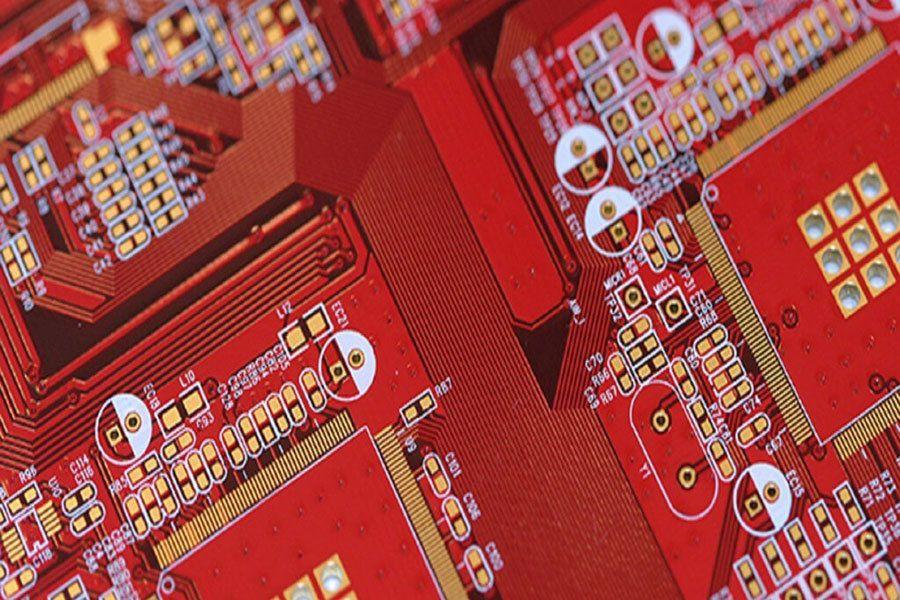
What material used in flexible PCB
Nowadays, flexible PCB (printed circuit board) develops so fast that its market share goes up and much progress has been made in terms of technology. The advent of new flexible PCB fabrication technologies drives flexible PCB to feature its advantages of lightweight, thinness, and flexibility, leading to its wide range of applications.
Flex PCB materials need to support multiple design and operational goals: static or dynamic flexing, ability to pass through standard assembly processes, and support for simple fabrication procedures with high yield. Flex PCB materials may seem exotic at first, but a relatively small material set is used to produce flex and rigid-flex PCBs at high volume. In this guide, we'll examine some of the basic properties of flex PCB materials and how they are used to build flex/rigid-flex PCBs.
While most standard PCBs have a fiberglass or metal base, flex circuit cores consist of a flexible polymer. The majority of flex PCBs have a polyimide (PI) film as a substrate. PI film does not soften when heated, but it stays flexible after thermosetting. Many thermosetting resins like PI become rigid after heating, making PI a superior material in flex PCB construction. Standard PI film does not have good resistance to humidity and tears, but choosing upgraded PI film mitigates these issues.
A flex PCB also requires an adhesive or special base material for its layers to attach. Manufacturers previously used adhesives only, but this method reduced the PCB's reliability. To resolve these issues, they developed adhesiveless PI that attaches to copper without an adhesive. This material allows for thinner designs with a lower risk of via breakage. Instead of using a solder mask to cover and protect a flex circuit, manufacturers use a coverlay film also created with PI. If you want the area on the flex pcb to be rigid, the manufacture can laminate a stiffer to that portion, but the signal cannot travel between the flex and the stiffer.
1. flexible pcb insulating substrates
The insulating substrate is a flexible insulating film. As the insulating carrier of the circuit board, selecting the flexible dielectric film requires a comprehensive investigation of the heat-resisting property, the coating performance, the thickness, the mechanical properties and the electrical properties of the material. Now commonly used in engineering is polyimide film, polyester commodity name Mylar) film and Polytetrafluoroethylene film. The general film thickness is selected within the range of 0.0127~0.127mm (0.5~5mil).
2. Flex pcb adhesive chip
The effect of the adhesive is to combine the film with a metal foil or an adhesive film and an overlay film. For different film substrates can be used different types of adhesives, such as polyester with a binder and polyimide adhesive sheet is not the same, polyimide substrate adhesive sheet epoxy and acrylic classification. The selection of the binder is mainly to investigate the fluidity of the material and its coefficient of thermal expansion. Non-bonded polyimide copper Foil Board, chemical resistance and electrical properties, etc. better.
Due to the low glass temperature of the acrylic adhesive, a large amount of contamination in the drilling process is not easy to remove, affecting the quality of metallization hole, and other bonding materials, such as disappointments, so, multilayer flexible circuit interlayer adhesive commonly used polyimide material, because with the polyimide substrate, its Q CTE (thermal expansion coefficient) consistent, The problem of dimensional instability in multilayer flexible circuits is overcome, and other performances are satisfactory.
3. flex pcb copper foil
Copper foil is a conductive layer covering the insulating substrate, which is then selectively etched to form a conducting line. The majority of this copper foil is made of rolled copper foil or electrolytic copper foil. The ductility and flexural resistance of the rolled copper foil is better than that of electrolytic copper foil, the elongation of the rolled copper foil is 20%~45%, and the elongation of electrolytic copper foil is 4%~40%. Copper foil thickness is the most commonly used 35um (1oz), also has a thin 18um (o.5oz) or thick 70um (2oz), or even 105um (30z). Electrolytic copper foil is formed by electroplating, the crystalline state of copper particles is a vertical needle, easy to form a vertical line at the edge of etching, is conducive to the production of precision lines; however, the needle-like structure is prone to fracture when the bending radius is less than 5mm or dynamic deflection. Therefore, the flexible circuit base material uses the rolling copper foil, its copper particle is, can adapt to many times around the curve.
4. flex pcb Cover layer
The covering layer is an insulating protective layer covering the surface of a flexible printed circuit board, which acts to protect the surface conductors and increase the strength of the substrate. There are two types of protective material for the outer shape, which are generally available for selection.
The first type is dry film type (covering film), the use of polyimide material, no adhesive directly with the need to protect after etching circuit board laminated mode. This covering film requires pre-molding before pressing, exposing the need to weld parts, and therefore cannot meet the requirements of the finer assembly. The second category is the photosensitive developer type. The first type of photosensitive development type is covered with a film coating machine after the adhesive pressure, through the photosensitive way to expose the welding part, to solve the problem of high-density assembly; The second is the liquid screen printing covering material, commonly used thermosetting polyimide materials, as well as photosensitive development type Flexible circuit board special solder paste ink. This kind of material can satisfy the requirement of fine pitch, high density assembling flexible plate.
5. flex pcb reinforcing plate
The reinforcing plate is bonded to the local plate of the flexible plate, and the flexible pcb film substrate is strengthened by the super-support, which facilitates the connection, fixation or other functions of the printed circuit board. Reinforcement plate material According to the use of different and sampling, commonly used polyester, polyimide sheet, epoxy fiberglass cloth board, phenolic paper board or steel plate, aluminum plate.
Material selection is determined by the combination of the electrical, mechanical bend requirements and cost considerations of a specific design. Electrical requirements, such as current carrying and impedance control, increase the flex thickness while high density designs require tighter bend capabilities of thin flex constructions.
The most common material choice used as a flex PCB substrate is polyimide. This material is very flexible, very tough, and incredibly heat resistant.
A flexible circuit is a printed circuit board manufactured using substrate that is naturally flexible. Flex circuits are typically manufactured using a polyimide (Kapton) material and one to multiple layers of copper. Popular suppliers of flexible materials are DuPont and Panasonic (we typically stock both). A flexible printed circuit board material will bend without snapping. However, the copper will likely crack if the bend causes a crease. A flexible circuit shouldn't be confused with a very thin "semi-flexible" FR4 board. A thin (<10 mil) FR4 board will flex, but because FR4 is brittle, will eventually snap.