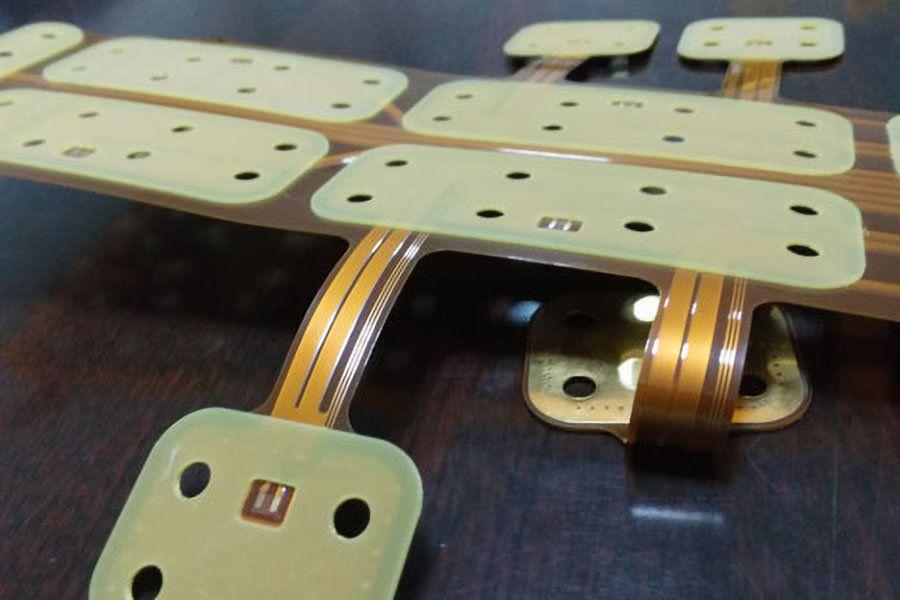
An Insight of the Flex PCB Manufacturing
Flex PCB manufacturing uses copper in a great amount for making a formation in an electrical connectivity track pattern. It brings together the components on the substrate of a Flex PCB. And for the proper and long-lasting functioning of these substrates, these copper should be properly coated. This prevents rusting and tarnishing due to oxidation.
A flexible printed circuit is using elastic laminate. The recyclables and qualities from the laminate are very important not just to its manufacturing process but additionally towards the performance from the finished circuit. The flexible laminate includes a performing foil as well as the dielectric substrates. The dielectric substances have two sorts which can be used for flexible printed circuits:
- A) Thermoplastics: The types of materials by which, after treating, will soften by warmth input, for example, polymers, polyester, fluorinated hydrocarbon, etc.
- B) Thermosetting Plastics: Materials, for example, polyimide, polyacrylate, etc.
Now, let’s evaluate the copper material, copper because the conductor is used and is available in foil form, while just about all flexible PCB is made of polyimide or polyester film. For a few of the special reasons, aramid and fluorocarbon films will also be used. The option of choice for a specific film is dependent upon numerous factors. These are highlighted below.
Cost-lower or cheaper flex circuits are made on polyester films that offer performance cheaper, however with a reduction in thermal resistance.
Super High-end flex PCB, especially individuals for military programs, are produced with polyimide films simply because they provide the best efficiency.
Aramid non-woven fiber material isn’t pricey and has a great mechanical and electrical property. The main problem is that this material will absorb moisture.
Fluorocarbons are a costly material as well as tough to handle. Nevertheless, it provides the best dielectric qualities. These components mostly use for controlled impedance programs.
Most of these methods are used to provide a protective coating to these copper connectors in Flex PCB manufacturing. Amongst these, the organic coating method has been used for the last many years. But unfortunately, this method is not without its share of disadvantages. It is not suitable for long-term usage, as it can cause an erratic deviation in solderability.
So far as application smart, the most famous material selection of Flex PCB circuits is a polyimide film. This is because of the typical performance and price factor of chemical qualities, electrical and thermal performance. These components may even withstand the temps in manufacturing soldering procedures. The fabric can also be utilized in wire insulation so that as insulation in motors and transformers.