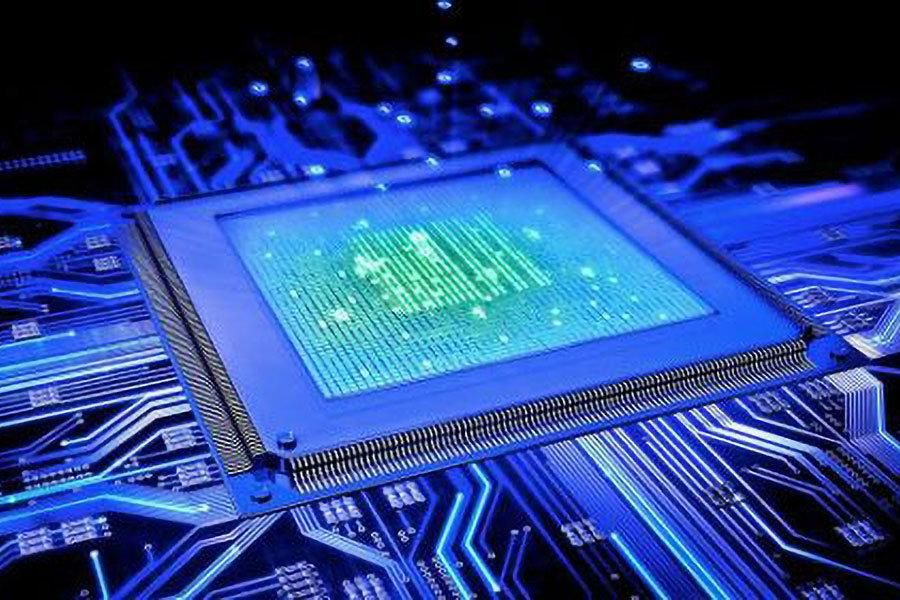
Types of HDI PCB Stackup
High-Density Interconnect (HDI) circuits are quickly replacing conventional PCB designing and fabrication techniques. Most compact and sophisticated electronic devices would not have been possible without the advent of HDI. It allowed circuits to become smaller and reliable, even in harsh environmental conditions.
Designing an HDI PCB is very different from designing and fabricating a conventional PCB that relies on Plated Through Holes (PTHs) for layer interconnections. Thanks to microvias, HDIs can be created with much more component density than a standard PCB. And like a typical PCB, HDI is designed using some set guidelines.
HDI PCB Stackup Types
There are two prevalent methods of dividing HDI stickups into different types. One is the IPC classification, which divides HDI Stackups into Types I to VI. Out of these six types, most commonly used are type I, type II, and Type III.
The other type of HDI stackup is M+N+M. Where M stands for the number of HDI layers, and N represents the number of layers in the core. For example, a 1+6+1 stackup would mean that the central core has six layers while one HDI layer on either side.
IPC Defined HDI Stackup Types
First, let’s take a look at the IPC stackup classification.
HDI Type I Stackup
Type I stackup only permits blind vias and PTH, and the blind vias cannot be more than a layer deep. They can originate from either the top or bottom surface. This is the simplest of HDIs that can be designed or fabricated, and consequently, the most limited type of stackup. It’s also the cheapest to fabricate.
One limitation of type I stackup is the layer count. For the PTH, the total aspect ratio has to be maintained below 10. That puts a serious limitation on layer count if you are not willing to increase PTH diameter. Because each extra layer adds to the board’s thickness, threatening the aspect ratio.
Another limitation is the presence of microvia in only one layer (one HDI layer). The diameters of PTH via pads increase with each new layer count (to maintain aspect ratio). Increased via pad diameter means less and less space on the surface for traces and components. Usually, microvias allow for finer traces and small diameter via pads. But this benefit gets seriously limited as the number of layers in Type I grows.
HDI Type II Stackup
Type II stackup allows for buried vias in the core, but the blind vias are still limited to just one HDI layer. Use of buried via help reduce the overall board thickness, which allows for smaller via diameters. Since smaller via holes allow for much more surface space, designers have more routing freedom. But due to just one HDI layer, the trace width still can’t be reduced.
The buried vias are drilled in the core before adding the HDI layer. Some fabricators allow for variations in Type II. These variations make them more suitable for certain circuit requirements that cannot be met by typical Type II stackup. One such variation is variable depth blind vias.
HDI Type III Stackup
The most commonly used HDI stackup, especially for high-density requirements, is Type III stackup. It allows for two or more HDI layers, with blind microvias in all HDI layers that can be staggered or stacked. They can also be stacked and staggered in accordance with buried via. Due to multiple HDI layers, this HDI stackup provides superior routing freedom in design. It also allows much thinner trace widths than either Type I or Type II. One limitation in Type III is of layer count if it uses PTHs.
One way to control cost in Type III stackups is to use staggered vias instead of stacked. Type III also allows the surface layer to be used for power or ground plane, leaving inner layers for signals.
HDI Type IV, V, and VI Stackup
These types are not as commonly used as the other three types. In them, type IV uses a passive core, which means that the core doesn’t have any electrical properties. It can, however, still be used for heat dissipation, shielding, or CTE management.
Type V is a coreless stackup. It uses plated microvias, and a conductive paste layer interconnect. The layers are co-laminated, so there is a single lamination step: no buildup or sequential lamination.
Type VI is also a coreless stackup. It doesn’t necessarily require plated microvias. And conductive interconnects can be made using dielectric piercing or antistrophic films as well. It can be co-laminated or sequentially build.
Other HDI Stackup Types
Though they are the derivatives of IPC stackup types, it is crucial to understand i+N+i Type of HDI stackup as well.
1+N+1
This can be considered a Type II HDI stackup. Since it allows for one HDI layer on either surface and requires one lamination step. The N refers to the number of layers in the core (usually FR4), while the ‘1’ refers to the copper foil (HDI layer) on the top and bottom surface of the core. So a 1+4+1 configuration has a total of six layers. The buried via is drilled in the core, so it would reach from layer 2 to layer 5 of this stackup.
2+N+2 and M+N+M
2+N+2 stackup type can be considered the most basic Type III stackup, with two HDI layers on both surfaces. This type also needs two sequential laminations. When the number of layers increases from two, M+N+M can be used to calculate the total number of layers. Sometimes, fabricators use the formula M+bN+M, to incorporate buried vias (b).
ELIC HDI PCB
Though it’s often considered very different, Every Layer Interconnect is sometimes also considered a type of HDI stackup. In it, any layer can be connected to any other using copper filled microvias.
Conclusion
Understanding the types of PCBs, their design guidelines, limitations, and price implications is essential. For the best results, you should consult the design guidelines of the fabricator and involve them in the design process as early as possible.
We are focused on building the technology for the future. It’s evident in our cutting-edge fabrication techniques and capabilities. With us, you can realize your most ambitious HDI pcb designs. We offer Every Layer Interconnect, assembly up to 68 layers, specialized microvias (telescoped, skipped, etc.), buildup flexibility, and highest quality high-frequency/low-cost material.
Whether you want ultra-thin flexible HDIs for wearables, or rugged, highly compact HDIs for harsh environment requirements, we can accommodate all your needs.