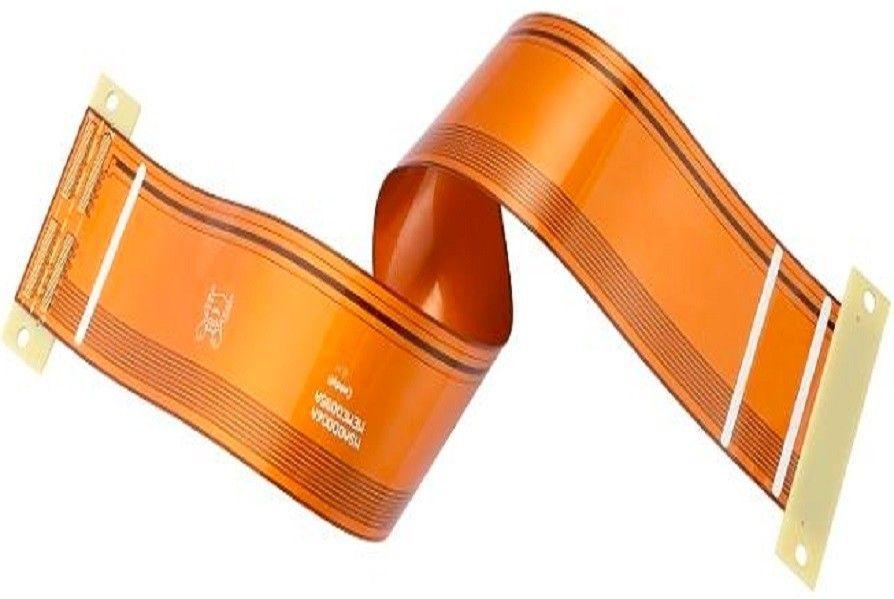
What is Flexible Circuit Technology?
Flexible circuit technology. It is one of the few technologies to have such a self-explanatory name. Flexible circuit technology was a revolutionary step in the world of PCBs, the backbone of electronic circuits. There was a time when it was considered a novelty in the industry; now, it's almost a necessity. You will find several electronic devices that can use this technology, and many of those would not have conceivable if it weren't for flexible circuit technology.
Flexible Circuit Technology
Before we take a more in-depth look into it, let's establish what flexible circuit technology is. Flexible circuits are mechanically flexible PCBs. They can be bent and flexed (to an extent). This mechanical fluidity allows them to be integrated into a number of devices where a conventional rigid PCB cannot be installed.
If we take a look at a very basic, single layer PCB, with relatively low component density, it can easily be converted to a flex design by replacing the conventional rigid core. But it’s not as simple as that. A PCB is much more than just its core and component placement. And even in a basic circuit, the component placement cannot be the same as a rigid board.
When you are working with flexible circuit technology, you have to give equal importance to the mechanical and electrical characteristics of the circuit — something you didn't have to do with a rigid PCB.
Rigid Circuit Technology vs. Flexible Circuit Technology
Rigid PCBs have been around since the inception of the first PCBs. First, PCBs were little more than hard boards to etch copper traces and drill holes to put and solder the legs of electronic components. But they have come a long way now. With technologies and advances like flexible circuits and rigid-flexes, PCBs have become even more commonplace.
Does that mean that the era of conventional rigid PCBs is over? Not exactly.
Just like Flex circuits have their specific applications, Rigid circuits have their own place in the electronics industry. The most fundamental difference between the two technologies would be simplicity.
If we discount the multilayer HDI construction that is complex for other reasons, a rigid PCB is relatively straightforward to design and fabricate, compare to a flex PCB. In a rigid PCB, you are not bound by the mechanical limitation of the substrate, and you have access to the whole real estate on both the top and the bottom of the PCB.
In a flex, you have to be careful with PTH and component placement. You can place neither within a bend area of the flex. Because if you do, it will undermine the uniformity of the copper distribution, which will result in fractures in the copper. If that happens, the circuit will either not work, heat up fast, or cause structural damage to the flex.
But there are applications where flexes are clearly superior, even considering the difficulty in design. For applications where the accommodating the circuit inside a particular housing (like a hearing aid) is the primary target, you don’t have any other choice than using a flex circuit.
In terms of cost, simple rigid circuit technology is much cheaper than flex technology.
Benefits and Limitations of Flex Circuit Technology
Mechanical flexibility is one of the most apparent benefits of flex PCB based devices. This allows so many options to the designer that a rigid PCB simply can’t. Like designing in 3D. With a rigid circuit, you are stuck in two-dimensional designs, which might not even let you fully utilize the available space. But if you are using flexible circuit technology, you can utilize the space in a much more efficient manner. Thus you can create a denser, more elaborate circuit, in a similar housing space, compared to what you could have designed with a conventional rigid PCB.
Another great benefit of flexible circuit technology is the dynamic flex. For application, where a circuit needs to be constantly bent (or have multiple bend cycles), there is simply not a feasible replacement for flex. If you connect two rigid boards using wires and connectors, the circuit integrity and potential life-span of the device would be very low.
When the flex circuit acts as a conductive-traces connector between two rigid PCBs or even between two different parts of the same rigid circuit, it eliminates the need for wires and connectors — thus eliminating many potential failure points in the circuit.
Flex circuits are also very light in weight. It’s mostly because of the laminates and the core material being light and flexible. But the reduced weight is also the result of a lighter copper layer and thinner adhesive layers (or no adhesive layers), this is mandatory to keep the flex, flexible.
But with all these great benefits, there are certain limitations to flex circuit technology as well (but most of them are being overcome, as the technology evolves).
The very first limitation is cost. Due to its materials, relative fabrication complexity, and assembly issues, flex is usually the costliest PCB solution. An excellent way to take care of this limitation is to design in rigid-flex.
Another limitation is the temperature handling capacity of the flex circuits. This usually limits the number of layers you can design in a Flex PCB. They have to be handled with relatively much more care, as they get easily damaged if they are bent the wrong way or a static flex (that is bent just to install) is bent repeatedly.
Conclusion
Like any other technology, Flex circuit technology has its benefits and limitations. Whether you choose to design in flex or rigid-flex depends upon the application of your circuit. A good way to eliminate the risk, reduce the cost, and get the best efficiency out of your flex circuit is to work with fabricators who have a lot of experience with this technology. If you work with us, you will not only have our years of fabricating a wide range of flex circuits, but also a wider range of material options, and an assembly line that is equipped to handle almost any design needs.