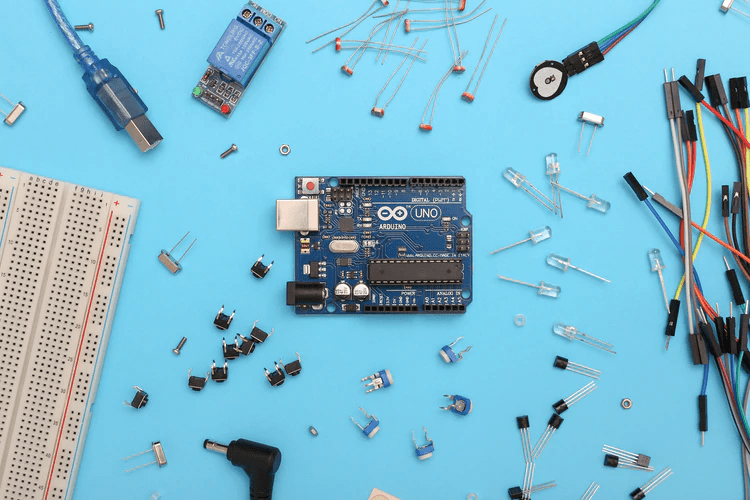
What You Should Know About Microvia Stackups
In PCB construction, we're always on the hunt for new technology advancements that will make our jobs easier and allow us to do more as designs get slimmer and denser. Microvia is one of these enhancements. These laser-drilled vias are tinier and have a distinctive aspect ratio from standard vias. High Density Interconnect circuit boards, often abbreviated as HDI PCBs, use microvias and stacked microvias to allow intricate interconnection in complex designs.
Microvias, stacked microvias, and via-in-pad structures allow for downsizing and can support massive pin-count semiconductors like those found in smartphones and tablets. Microvias minimize the number of layers on printed circuit boards while increasing routing density and removing the requirement for through vias. In this post, we’ll discuss what microvias are, the advantages of a microvia PCB, and different stack-up types.
Understanding Microvias
A microvia is a blind structure with a maximum aspect ratio, i.e., the ratio between the depth of the hole and its width, of approximately 1:1. It terminates on a target land with a total depth of no more than 0.25 mm from the capture land foil structure. Microvia PCBs most commonly have the same depth as the dielectric thickness or the distance between both layers.
In typical HDI PCB fabrication designs, the depth or dielectric thickness between the two layers is usually 60 to 80 microns. Hence, the size of the microvia hole needs to be within 80 to 100 microns. Considering these values, this provides an aspect ratio of approximately 0.6:1 to 1:1. As the size of the dielectric thickness increases, the size of the microvia must increase as well.
Why Are microvia Useful?
As technology improves, the goal in PCB construction is to fit more trace routing into compact dimensions. As a result, blind and buried vias, along with vias embedded in surface mount pads, have become popular.
Nevertheless, due to the additional drilling procedures required, blind and buried vias are more challenging to construct, and the drilling can leave debris in the holes, culminating in manufacturing problems. Regular vias are also typically too big to be integrated into modern devices' tiny surface mount pads. The microvia, on the other hand, can assist with all of these issues.
Microvias are less difficult to make than smaller blind or buried vias. Microvias integrate into narrower surface mount pads, rendering them ideal for electronics with a high pin count, such as ball grid arrays (BGA). Due to their reduced scale, microvias can lead to improved trace routing across them. Moreover, they can also assist in minimizing EMI and alleviating additional signal integrity concerns.
Microvia Stack-up Types
Microvias are made in the form of cones, making copper plating of the via sides simple. A microvia can only pass through 2 adjacent layers before stopping. If a circuit design calls for a via to pass through many layers, multiple microvias must be placed in the appropriate order.
Constructing stacked microvias can be an expensive and time-consuming procedure from a fabrication standpoint. The most typical design for boards that need one microvia over the other is two microvias. The maximum number of microvias that can be stacked is four. Four microvias, on the other hand, are rarely used in PCB fabrication due to their expensive cost.
A blind microvia is one that penetrates the board from the outer layer and goes through to the internal layer before terminating. If the microvia penetrates two layers at once, it can be referred to as a skip via. Finally, a buried microvia is a microvia that links two interior layers of a PCB. To incorporate a buried microvia in a PCB design, the layers containing the apertures must be drilled before the top layers are attached.
Microvias are not just limited to the two layers we mentioned before. They can be present in the inner layers as well, and having more than one layer of microvias is what dictates the different types of microvia stack-ups as defined in the IPC specifications.
IPC-2226 Type I (1 + n + 1)
The type I configuration of microvia PCB stack-ups contain a single microvia layer on either one of both sides of the core, and it uses both plated microvias and plated-through holes or PTH for interconnection. Thus, in effect, it employs only blind via holes and not buried via holes.
IPC-2226 Type II (1 +n +1)
The type II configuration of microvia PCB stack-ups is similar to type I in the sense that they contain only one microvia layer on one or both sides of the core. It uses both plated-through holes and plated microvias for interconnection. Unlike type I, these structures use both buried and blind via holes.
IPC-2226 Type III (2 + n + 2)
The type III configuration of microvia PCB stack-ups is slightly more complex than type I and type II structures. This stack-up or build contains at least two layers of mircovias on either one or both sides of the core. It also uses both plated microvias and PTH for interconnection, as well as both buried and blind vias.
Microvias that originate on the surface layer do not need to be filled, while buried microvias would be filled with various materials according to the application. For communication between both the stacked vias, electroplated copper usually fills in the microvias. Staggering microvias and interconnecting them with short traces is yet another way to link them across the layer stack.
Last Thoughts
Microvias are a more sophisticated HDI PCB fabrication technology, and if your circuit doesn't require them, you'll want to go with normal vias to save money. However, if your design is complex and you require additional space, research whether microvias can help. Before designing a microvia PCB, it's usually a good idea to consult with your fabricator to see what they can do.
HDI PCB fabrication has evolved into a systematic collection of processes that necessitates specialized knowledge and equipment. HDI PCB design requires the help of an HDI PCB designer that understands the complexity of this cutting-edge equipment and can decide on the appropriate HDI PCB microvia stack-up for your product.
Being one of the first manufacturers to deliver HDI PCBs in bulk to clients, Hemeixin's expertise and commitment to providing a holistic service to our customers contribute to shortening the production process, resolving early design issues, and delivering a cost-effective, high-quality product. To acquire an online quote for your microvia PCB, visit this page.