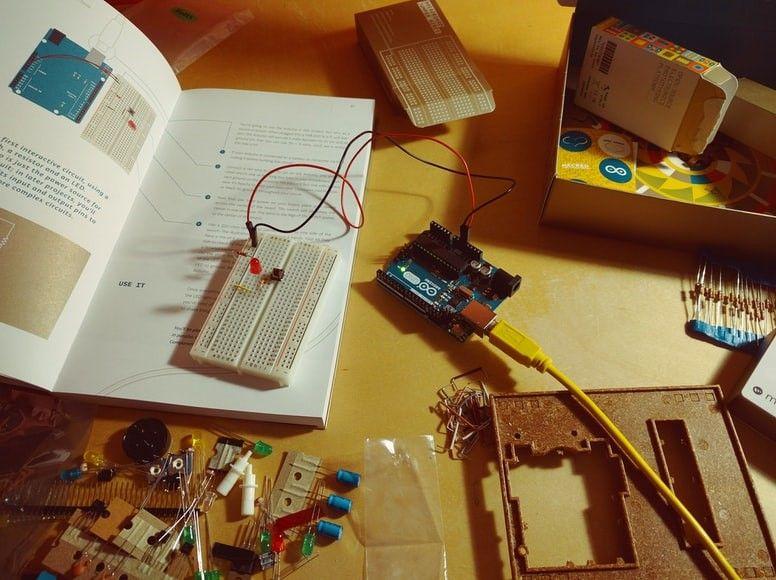
What is HDI PCB Stackup?
Modern society is moving away from the paradigm of building electronic systems that are only functional. As a result, the notion that our goods and systems will be "smart" swiftly becomes the standard for future devices. A logical assumption would be that printed circuit boards (PCBs) have been around for quite some time, based on the widespread usage of electronics and printed circuit boards (PCBs) in our everyday life. This, however, is not the case at all. Realistically speaking, we have been on an evolutionary road for more than a century, leading us to the printed circuit boards (PCBs) developed and manufactured today.
Throughout the years, several modifications and improvements have been made to the idea to make it even better. Modern electronics benefit from the advancement of materials and computerization, which has allowed the PCB to evolve into multilayered boards, flexible circuits, rigid-flex hybrid boards, and HDI PCB (miniaturized designs) now common in the industry.
High-Density Interconnect (HDI) Overview
To meet the growing demand for more powerful devices, it became essential to pack more electrical circuitry into smaller and more compact electronic devices—high-density interconnect, or HDI was then traditionally pushed forward by the dual dynamics of increased functionality and smaller package size. As Happy Holden, the HDI's founder, states in The HDI Handbook, high-density interconnect (HDI) challenges the conventional method of doing "the same things in the same manner, just smaller."
What is HDI PCB Stackup?
Stackup is the term used to describe the collection of copper and insulator layers used to construct a printed circuit board (PCB) before the final design of the board is created. There is a need for compacted electronic goods in the electronic industry, so PCB layer stackup is critical. It is possible to achieve more energy distribution capability by using additional layers and supporting signals at a higher speed, eliminating electromagnetic interference, and avoiding cross-interference.
Assembly Approaches Used by HDI PCB Manufacturers
When constructing boards with high-density packages, PCB manufacturers often use one of the following assembly approaches:
• Standard Lamination (Vias or Plated Through-Holes)
• Sequential Lamination (Plated Through-Holes, Blind, and Buried Vias)
• Lamination Buildup (Microvias)
Standard lamination with plated through holes and vias is less expensive for 28 layers than custom lamination. Routing would be challenging if you had a significant number of huge BGAs with a pitch of less than one millimeter.
On the other hand, sequential lamination costs are higher than standard lamination. Compared to through-hole vias, the sequential lamination with blind and buried vias has a simpler model, shorter stubs, and a lower diameter. The dependability of the stackup Type and the minimum trace lengths restrict the number of layers that may be added to it.
Finally, due to the apparent constraints of the two assembly procedures described above, lamination stacking through micro vias PCB is the most practical solution. Micro via PCB has thinner trace widths and vias with smaller diameters, allowing for higher routing density and fewer layers. Using micro vias strategically and adequately positioning them on the circuit board may minimize the number of layers while simultaneously increasing routing space. Designing large fine-pitch BGAs with a 1mm or less pitch is the most effective solution for this application.
As a result, micro vias are advantageous because they improve signal integrity, which is not achievable when utilizing conventional materials. Furthermore, the micro vias are incompatible with standard and sequential assembly methods.
Types of HDI PCB Stackup
Printed circuit board (PCB) fabricators may use HDI PCB stack-up types I through VI, defined by the IPC-2315 standard from the Institute of Printed Circuits (IPC). Types IV, V, and VI are more costly to produce and are not often used for high-density printed circuit boards (PCBs) with routing and BGA breakout issues. Although plated through vias are not necessary for flex PCBs that adhere to the HDI standard, they may be utilized to distinguish HDI stack-ups from other types of PCBs.
HDI Type I Stackup
Only blind vias and PTH are allowed in Type I stack up, and the blind vias can't be more than one layer deep. Since it is the most basic HDIs that can be developed or built, it is also the most restricted form of stack up and the least expensive to manufacture.
The number of layers in Type I stack up is one of its limitations; however, the entire aspect ratio must be kept below 10 for the PTH to function correctly. Suppose you do not want to extend the diameter of the PTH. In that case, you will have a significant constraint on the number of layers you may have because each additional layer increases the thickness of the board, the aspect ratio is threatened.
Another constraint is the existence of microvias in just one layer (one HDI layer). The diameters of PTH through pads grow in size with each additional layer count added (to maintain aspect ratio). As the diameter of the via pad increases, the amount of surface area available for traces and components decreases. Microvias are often used to create more delicate traces via pads with smaller diameters. Nevertheless, as the number of layers in Type I increases, it becomes more limited.
HDI Type II Stackup
Type II stack up allows for the inclusion of buried vias in the core, although blind vias are still restricted to a single HDI layer. The use of buried vias helps to minimize the overall thickness of the board, allowing for lower via sizes to be used. Designers have more routing flexibility since smaller via holes allow for much more surface area; however, the trace width cannot be reduced because there is only one HDI layer.
Before installing the HDI layer, the buried vias are drilled into the device's core. Type II is subject to change according to certain fabricators. These modifications are more appropriate for particular circuit needs that a typical Type II stack-up configuration cannot provide.
HDI Type III Stackup
Known as the most expensive, Type III stack up is the most often used HDI stack up, particularly for high-density needs. With blind microvias in all HDI layers that may be layered or staggered on top of one another and in line with the location of the buried via, it allows the use of two or more HDI layers. Due to the various HDI layers, this HDI PCB stackup enables more routing flexibility in the design phase. Moreover, significantly narrower trace widths than either Type I or Type II is also possible.
If you employ PTHs, there is a limitation to the number of layers in Type III. One method to keep costs down in Type III stackup is to utilize staggered vias rather than stacked ones. Type III additionally allows for using the surface layer as a power or ground plane, with the interior layers remaining for signal transmission.
HDI Type IV, V, and VI Stackup
Type IV, V, and VI are not as often utilized as the other three categories, which is understandable. Type IV employs a passive core, which indicates that the core does not have any electrical qualities, unlike the other types (Type V and VI. The material may still be utilized for CTE control, shielding, and heat dissipation.
Besides that, Type V is a stackup that does not have a core. It makes use of plated microvias as well as a conductive paste layer for interconnecting the components. There is just one lamination phase since the layers are co-laminated; there is no need for buildup or sequential lamination. Type VI is similarly a coreless stack up, as is Type V. In addition, conductive interconnects may be created by piercing or antistrophic films dielectric and can be built in two ways: co-laminated or sequentially.
The Final Cut
It is critical to understand the different types of HDI PCB stack-ups and their design rules, limits, and price variations. We hope you now have a thorough understanding of the HDI PCB stackup for deciding on an appropriate board for your next project. Want to ensure the highest dependability and performance? Join hands with a premium manufacturer like HemeixinPCB.
We'd like to hear from you!
HemeixinPCB
Wanxia Industrial Park, Tongfuyu Industrial Area,
Shajing Town, Bao'an District, Shenzhen, China
+86-755-2758-6529
This email address is being protected from spambots. You need JavaScript enabled to view it.