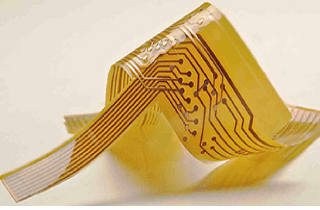
Applications of Flexible Printed Circuit Boards
Flexible PCBs, or flex PCB, were specifically designed to provide relative mechanical flexibility to a circuit, something that rigid PCBs don’t have. This allowed circuits to shrink in size, form, and weight (which helps increase its reliability in mechanically harsh environments).
Flexible circuits don’t just enhance the characteristics of the circuit itself; they improve the device they are in as well. Some of these devices wouldn’t even exist if wasn’t for flex PCBs.
Applications of Flex PCB
Before we dive into specific applications of flexible circuits, it's essential to understand the different classes defined in IPC-6011 (IPC-6013 for Flex PCBs). PCBs of different classes have various uses.
Flex PCB Classes
There are three main classes:
Class 1 (Limited Life Devices)
Class 1 Flex circuits are created for devices that are supposed to have a limited life expectancy. These flex circuits are relatively low-quality, less intricately designed, and not as reliable as other classes. Many manufacturers nowadays don’t even fabricate Class 1 flex circuits because of their limited applications.
Class 1 flex applications include LED circuits, flashlights, flexible (or tiny) remote controls for various devices, and some instruments. Most of these devices are static flex. For these, the flexible PCB is bent once (or a few times) throughout its life.
Class 2 (Reliable Devices)
Class 2 Flex PCBs find their application in relatively more reliable devices. Their design and fabrication requirements are consequently stricter. For example, a class 2 Flex PCB cannot have a solder penetration exceeding 5 mm; only one void is allowed per hole and not exceeding 5% of the hole size, and restrictions regarding minimum internal annular ring size, etc.
These design and fabrication restrictions make sure that a Class 2 flex PCB can be used for long-life and relatively more reliable devices. These circuits can also handle harsh environments, jerks, and other mechanical shocks better than Class 1 flex PCBs.
Some typical Class 2 flex applications include cell-phones, cameras, laptops, and wearable electronics. Unlike class 1, class 2 flex circuits can be used for dynamic flex applications, where the circuit might have to go through a lot of flex cycles.
Class 3 (Highly Reliable Devices)
Class 3 flex PCBs are produced with even higher quality and reliability in mind. The most common applications of these types of Flex PCBs are in the medical, military, and automotive industries.
Class 3 design and fabrication rules are even more detailed and strict. You can’t have any voids in the vias, plating penetration cannot exceed 0.3 mm, and conductor width cannot be reduced by more than 20%, among many other rules.
Class 3 applications include pacemakers, ABS circuitry, drones, and other medical implants, etc. They can be both static and dynamic in nature.
Other Common Applications of Flex PCB
Some of the most common places you may find are:
Smart Phones: Since flex PCBs offer a significant reduction in device size, as well as dynamic flexibility for smartphones that bend, Flex PCBs are greatly in demand for cell phone circuits. The use of flex circuits for cell phones in place of rigid PCBs helped reducing their width by almost 40%.
Aerospace applications: Flex PCBs (exclusively class 3 Flex PCBs) are used in many aerospace applications, especially in the satellites and space probes where the designers have to maintain a tight balance between reliability and weight.
Flex screens: With the advent of the first LCD and now LED, displays and screens have also shrunk in size. Another relevant application that is being developed is flexible screens, which may act as “digital paper” in the future. This is based primarily on flex PCBs. It's a challenging avenue because the screens need to be transparent.
Wearable electronics: Wearable electronics were limited to high-tech watches up until a decade ago. But now, smartwatches are very commonplace. They provide the functionality of a complete smartphone, and in some cases, act as health monitors too. Their core design is based on flex circuits.
Keyboards: Computer and laptop keyboards are also one of the most common applications of Flex circuits.
Hearing aids: Many high-end hearing aids are built around flex PCB. They are very lightweight and can handle the constant movement and relative exposure.
In-body implants: In-body implants are very intricately designed, and they need to be able to withstand body heat and exposure to elements inside the body. Many in-body implants depend upon flex PCBs, especially in places where heat dissipation from the circuit can damage the tissue. These implants are made with unique materials and particular design considerations in mind.
Flex PCB as Connecting Circuits
Another great application of Flex PCBs is their use as connecting circuits, where they replace the conventional wire and connector system. This reduces a circuit’s weight and makes it much more reliable by eliminating many potential failure points.
In most such applications, Flex PCBs are locally rigidized to make them usable for ZIF connections. This type of circuit may or may not be different from a pure rigid-flex that is fabricated as a single circuit. Nevertheless, it has excellent application in devices and circuits where a very high degree of reliability is needed, along with reducing the packaging size.
Conclusion
These are just a few of the examples of the applications of Flex circuits. There are millions of devices that partially or fully depend upon flex circuits. But as you might have gathered, different applications require different degrees of fabrication care and design consideration. This is why you must work with fabricators that have the experience and equipment needed to realize your PCB design, no matter how complicated it is.
But that doesn’t mean that you should design with only the application needs in mind. A good designer always keeps the practicality of FLEX pcb fabrication in mind. Because if you don’t, you will waste too much time and resources going back and forth with the fabricator. It's better to go over the design guidelines and your ideas with the fabricator, before completing your design.