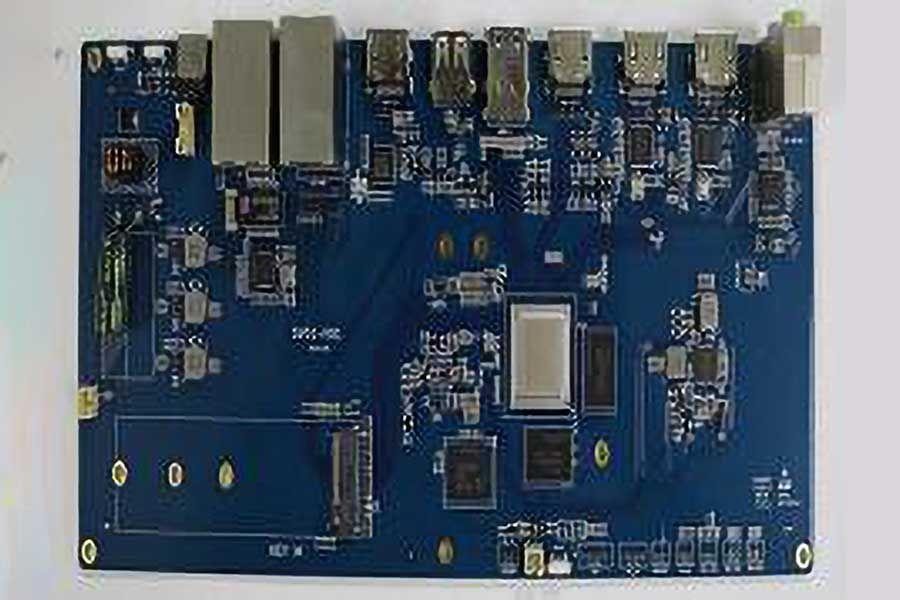
What are the differences between surface mount soldering and through hole soldering
PCB configurations are still much dependent the nature to components to be used. Their shapes and pattern rely on the nature of resistors, capacitors, and diodes that will be deployed for the electric configuration of the board. Normally, PCB manufacturers will either mate long leads into plated through holes on the board or attach them to the PCB surface only. While the former is regarded as through-hole soldering, the latter is often described as surface mount soldering. Knowing which one is better is a matter of comparison and serious evaluation.
In this article, comparisons between both soldering methods will be made. This will provide PCB designers insight into the applicability of each method.
Before making comparisons of their features, it’s pertinent to provide a brief description of both soldering method.
Through-Hole Technology
Through-hole technology is an older board soldering technology. It ensures that the accidental creation of bridges between the pins on a single component is much avoided. In most cases, spacing is encouraged to ensure electrical efficiencies. Typically, the spacing between the hole centers is around 0.100”. The value can be greater than that value. For several decades, through-hole technologies were adopted in the development of almost every PCB found in electronic devices. When deployed, leads on electrical components are inserted into the drill holes on PCB and subsequently soldered to pads located on the opposite side of the board.
This soldering method is much reliable. This is because the mechanical bonds on the board are made much stronger. Meanwhile, the presence of holes in PCB often creates limitations in terms of the existing routing areas which are relevant for tracing signals on the layers. On multi-layer boards, they are usually found beneath the top layer. Those drawbacks are part of the major issues that motivated advancement into the use of Surface mount technology.
Surface Mount Technology
No matter the reasons made to justify the use of through-hole components, it’s pertinent to note that surface mounted components offer unrivaled benefits for users. It offers a greater level of component density and processing power. This helps fit everything within a much smaller and lighter overall PCBA. Since there are huge demands for compact PCBs, the necessity for making efficient use of available surface area also rises. SMT technology becomes a necessity.
As against drilling of holes, SMT ensures electrical components are mounted directly to the surface of PCB. There is no need for mating holes. They either accommodate smaller leads or doesn’t accommodate it at all. Since surface-mount devices (SMDs) requires lesser drilled holes, the electrical components become more compact and higher circuit densities are more encouraged. This innovation is more crucial is this era that every electronics are growing complex and compact. It’s the budget’s friendly and easier to use.
Difference between Through holes and Surface Mount Technology include the following :
- SPACE EFFICIENCY: Surface Mount Technology optimizes spaces better than through holes. Often, they utilize available small spaces for assembly of electrical components. On the flip side, Through-hole technology remains stuck to the assembly of passive and active electrical components on larger boards. Since the amount of space utilized by them varies, packing density associated with each technology also differs.
- MOUNTING PROCEDURES: Surface mounting technology is not associated with leads. Whereas, through-holes are much related to leads. They support the configurations of lead wires on drilled holes. While the surface mounting technology allows mounting of electrical components onboard surface, the through-hole technology supports the drilling of boards for mounting the components. Because of the easiness in assembling electrical components through SMT, board designers thus promote assembly automation using the method. This development thus promotes the mass production of board assembled through SMT. Nevertheless, it’s worthy to note that soldering and de-soldering of through-hole components are much easier than that of SMT.
- COST OF PRODUCTION: Because expenses of acquiring SMT assembly machines are high, the overall set up cost of the machinery board is much expensive than the through-hole method. Though SMT is typically expensive on the machinery set up aspect, the capital required for producing it is much more budget-friendly. The machinery setups are necessary since soldering of SMC is quite tough through manual soldering.
- COMPONENT BULKINESS: Through-hole mounting is significantly important for large, bulky components. They are a good choice for components that will be exposed to regular mechanical stress, high power, and even high voltage parts.
- PERFORMANCE: With the help of SMC higher performance circuit can be made in small size which is a prime requirement today. Pin count of component is increased greatly in SMT as compared to old through-hole, for example, the micro process used today in computers PGA, FPGA, etc.
- PRODUCT COMPACTNESS: Size of through-hole component is larger than surface mounting components. In SMT, components can be mounted on both sides of PCB, this is not possible in through-hole. Therefore, the Surface mounting component has made the manufacturing of smaller applications possible. This, however, seem impossible with through-hole technology. The pin count is higher in SMT than in through-hole technology.
- EXPERTISE LEVEL: The design, production, skill, and technology that SMT demands is quite advanced as compared to through-hole technology. Such a level of advancement makes it surface mounting technology a preferable choice to numerous printed circuit
CONCLUSION: Both surface mounting and through-hole soldering technology are much relevant in today’s board manufacturing processes. Though both boards differ in almost every aspect, it’s still necessary to note that they are relevant in various fields. The decision as to which method to use will be determined by an individual or company nature of projects i.e. electrical devices to be designed and built.
Perhaps you need to further information about HDI rigid-flex and PCB assembly, don’t hesitate to contact Hemeixin at This email address is being protected from spambots. You need JavaScript enabled to view it.. Do you need to know the market price for the product? Get a quote here: https://pcbonline.hemeixinpcb.com/