Montaje de Circuito Impreso
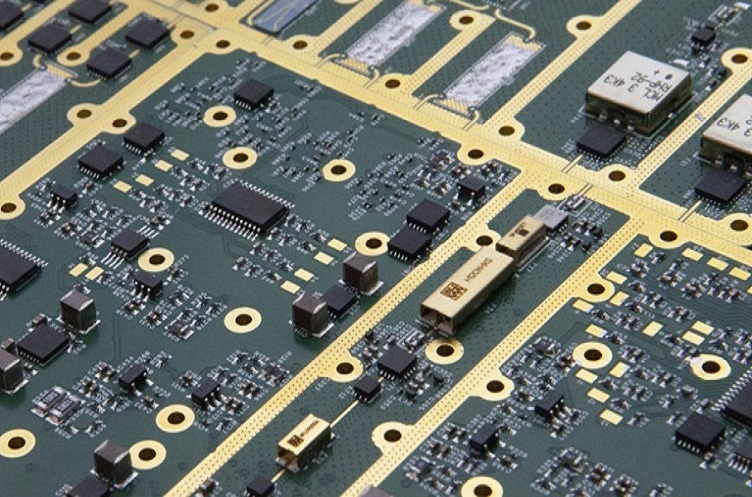
circuit board assembly Design Guide
La primera etapa del proceso de montaje de placas de circuito impreso consiste en aplicar la pasta de soldadura sobre la superficie de la placa. El objetivo principal es rellenar los orificios con la cantidad adecuada de pasta de soldar para poder fijar posteriormente los componentes eléctricos. La capa de soldadura debe terminar en los orificios, mientras que la superficie plana de la PCB debe permanecer intacta. Por tanto, es obligatorio aplicar una técnica muy selectiva para rellenar orificios de distintos tamaños con el grosor de película adecuado. Una de las técnicas más utilizadas es la impresión de pasta de soldadura, que representa una técnica de uso estándar en nuestra planta de producción.
Montaje SMT
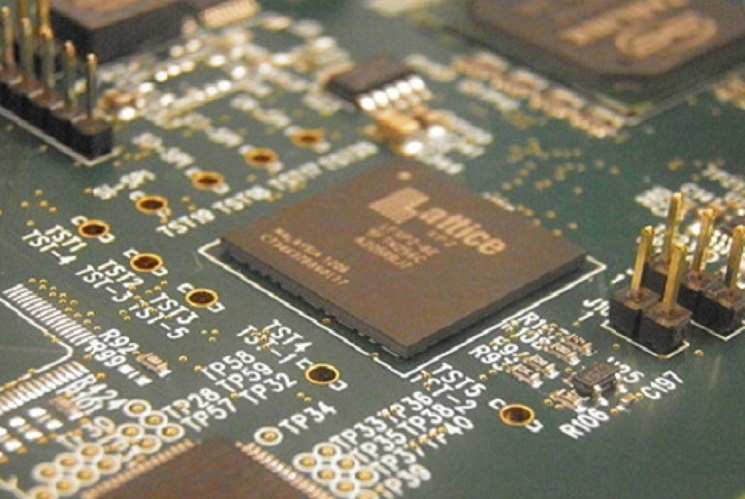
La tecnología de montaje superficial (SMT) es el proceso más utilizado en la industria cuando se trata del montaje de PCB de montaje superficial (SMT). No en vano, permite montar componentes directamente en la placa de circuito impreso de montaje superficial. La técnica se presta a la miniaturización de los ensamblajes, que está a la orden del día. Además, el ensamblaje SMT (montaje superficial) es conocido por su gran resistencia mecánica. Las placas de circuito impreso SMT son la opción preferida para circuitos de alta velocidad.
El montaje con tecnología de montaje superficial es una técnica en la que los componentes eléctricos y electrónicos se montan directamente en la superficie de una placa de circuito. Los componentes eléctricos y electrónicos que siguen esta técnica de montaje se conocen como dispositivos de montaje superficial (SMD). Esta tecnología minimiza los costes de fabricación y aumenta la eficiencia.
En Hemeixin, tenemos más de 15 años de experiencia en el montaje SMT de PCB. Con un proceso de montaje SMT automatizado, nuestras placas garantizan un rendimiento óptimo en las aplicaciones más exigentes.
Hemeixin ofrece a sus clientes décadas de liderazgo y experiencia en tecnología avanzada de montaje de placas de circuito impreso, con procesos probados y una completa gama de servicios. Desde la creación de prototipos, la mezcla de alto volumen bajo a la fabricación global de alto volumen, ofrecemos servicios de montaje de placas de circuito impreso en China.
Hemeixin es un líder reconocido en la producción de PCBA y SMT y desarrolla soluciones para nuestros clientes utilizando lo último en montaje de PCB y tecnología de montaje superficial. Las capacidades incluyen soporte para:
- 01005 componentes, BGAs de paso fino y alto recuento, Package on Package (POP), Chip on Board, fibra óptica, microelectrónica de RF, conectores a presión
- Procesos híbridos (estaño-plomo y sin plomo), agujeros pasantes, soldadura por ola y selectiva, reflujo a una y dos caras, cuerpos anchos y placas base.
- Montaje rápido de prototipos, certificación de conformidad con RoHS, revestimiento de conformal y parileno, marcado por láser
- Inspección y pruebas con los últimos equipos de SPI, AOI, sonda volante y rayos X.
- Pruebas eléctricas integrales y desarrollo de sistemas de prueba para escaneo de límites, pruebas en circuito (ICT), pruebas funcionales y pruebas de quemado (BIT).
Montaje de prototipos de PCB
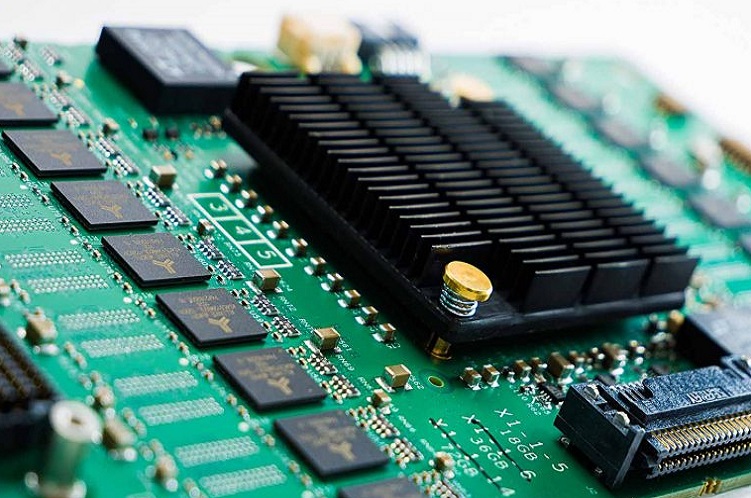
Los prototipos de placas de circuito impreso (PCB) se utilizan para reducir el número de errores o defectos en el diseño de una placa de circuito en una fase temprana.
Los prototipos de placas de circuito impreso (PCB) se utilizan ampliamente para reducir el número de errores en el diseño de una PCB. Estos prototipos ayudan a los fabricantes de equipos originales (OEM) a analizar los puntos fuertes y débiles de sus circuitos propuestos. La creación de prototipos ayuda a los fabricantes a ahorrar costes que, de otro modo, se gastarían en rectificar defectos y minimizar las retiradas de productos. Por este motivo, la mayoría de las empresas prefieren invertir en un prototipo de montaje de PCB antes de la producción de grandes volúmenes. Asociarse con un proveedor de servicios de montaje de PCB experimentado como Hemeixin Assembly les ofrece varias ventajas. Podemos encargarnos del montaje de prototipos de PCB en cantidades de 1 a 100 placas.
Aspectos destacados de los servicios de montaje de prototipos de PCB de Hemeixin Assembly
En Hemeixin Assembly, hemos adquirido capacidades que nos permiten servir mejor a nuestros clientes. Todos estos años, hemos trabajado en varios proyectos de montaje de PCB prototipo complejo, y creemos que las siguientes capacidades nos han ayudado a servir mejor a nuestros clientes.
Servicios de ingeniería de circuitos impresos: Podemos proporcionar prototipos de ensamblajes de PCB para diseño para fabricación (DFM) y diseño para pruebas (DFT). Además, podemos realizar análisis de los efectos del modo de fallo del proceso (PFMEA) e idear planes de control.
Servicios de montaje de prototipos de PCB: Estamos especializados en los siguientes servicios de montaje de prototipos de placas de circuito impreso.
- SMT: Podemos suministrar montajes de PCB de montaje en superficie de una cara y de doble cara indiferentes especificaciones.
- Agujero pasante chapado: Ofrecemos montaje de agujero pasante chapado con soldadura selectiva.
- Conjuntos mixtos: Trabajamos a menudo en proyectos que implican montajes mixtos: montajes con orificios pasantes y SMT y electromecánicos.
- Además, también apoyamos proyectos de introducción de nuevos productos (NPI).
Pruebas de PCBA: Todas las pruebas funcionales de PCBA se realizan internamente en nuestras instalaciones bien equipadas en China. A lo largo de los años, hemos invertido en varios accesorios y equipos de prueba, lo que nos ayuda a garantizar la calidad de PCBA. Actualmente, ofrecemos los siguientes tipos de servicios de pruebas de PCBA:
- Pruebas con sonda volante, incluida la prueba de límites
- Pruebas funcionales, incluidas pruebas a nivel de sistema y de placa
Capacidades generales de montaje de PCB: Nuestras capacidades generales de montaje de PCB no se limitan a estas:
- RoHS, con plomo, limpio y sin química
- Componentes de placas de circuito impreso, incluidos varios tipos de QFN, BGA, CSP, POP, 01005, 0201,08004 y componentes de ajuste a presión en pequeñas cantidades.
- Agujero para pegar
Montaje de PCB llave en mano
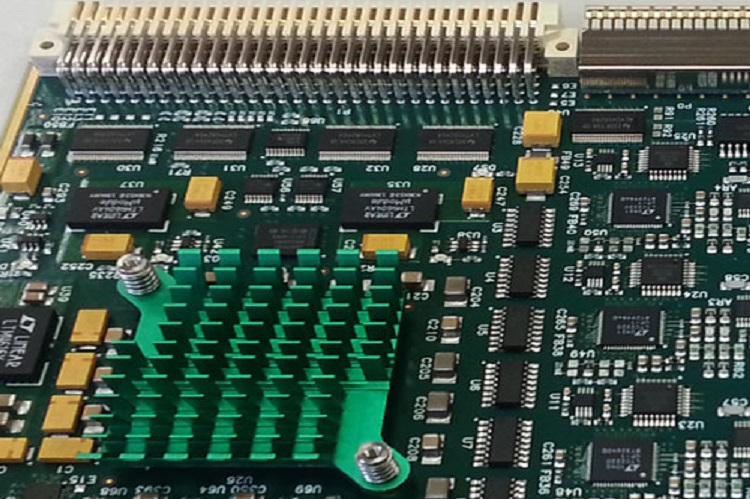
La fabricación de PCB con la máxima calidad es el corazón de Hemeixin Electronics Co., Ltd. Nos especializamos en varios tipos de proyectos de montaje de PCB, incluyendo el montaje de PCB llave en mano. Con nuestros servicios de montaje de PCB llave en mano, nos encargamos de todos los aspectos de la fabricación de PCB. Ofrecemos un montaje de PCB llave en mano rápido y fiable, ya que somos expertos en la adquisición de componentes, montaje, pruebas, entrega, servicio postventa y soporte de garantía.
Hemos trabajado con pequeñas empresas de hardware de nueva creación y grandes compañías de defensa, y una cosa que suelen necesitar es ayuda para navegar por la cadena de suministro de la electrónica y el panorama de la fabricación. Si usted no está involucrado en la industria, los servicios de fabricación de PCB pueden parecer opacos y difíciles de navegar, al igual que muchos otros servicios especializados.
Por lo tanto, es frecuente que los clientes busquen un fabricante que pueda ayudarles a guiarles a través del proceso de producción. Los servicios de fabricación de PCB llave en mano, los servicios de montaje de PCB llave en mano y los servicios de fabricación por contrato pueden ayudar a guiarle a lo largo del proceso asumiendo muchas de las importantes tareas de gestión necesarias para completar una tirada de fabricación. A veces, tiene mucho más sentido contratar estos servicios a través de su empresa de diseño que a través de un fabricante. Con un enfoque de proveedor único, podemos asumir cualquier proyecto complejo y entregarlo en un plazo breve, sin comprometer la calidad. Como forma líder de montaje electrónico, los servicios de montaje de PCB llave en mano aportan varias ventajas a los clientes.
- Nuestro montaje de PCB llave en mano es una forma rápida y eficaz de montaje electrónico. No tiene que preocuparse de gestionar varios proveedores, ya que nosotros nos encargamos de toda la fabricación.
- Con nuestros servicios completos de montaje de placas de circuito impreso llave en mano, podrá crear y perfeccionar prototipos de forma más rápida, sencilla y rentable.
- Estamos equipados para trabajar con pequeñas series de placas (con orificios pasantes, de montaje en superficie, mixtas) o con series de producción completas.
- Disponemos de redes de cadena de suministro verificadas para apoyar todo el proceso de montaje llave en mano. Con las soluciones integrales de un único proveedor, también puede obtener importantes ahorros de costes.
- Contamos con un equipo de personal altamente cualificado con experiencia en el montaje llave en mano de placas de circuitos impresos. No sólo ayudan a satisfacer sus expectativas en términos de calidad, sino también completar sus proyectos más rápido.
Ofrecemos presupuestos instantáneos para su pedido de montaje de PCB llave en mano y no tendrá que esperar mucho para saber cuánto le costará el pedido. Además, puede ver el estado de su proyecto en tiempo real. Esto le ayuda a supervisar la fase de fabricación de PCB. Con un único punto de contacto y servicios flexibles, el ensamblaje electrónico llave en mano completo de Hemeixin Assembly satisface las necesidades únicas de pequeñas empresas, grandes corporaciones y emprendedores.
Montaje BGA
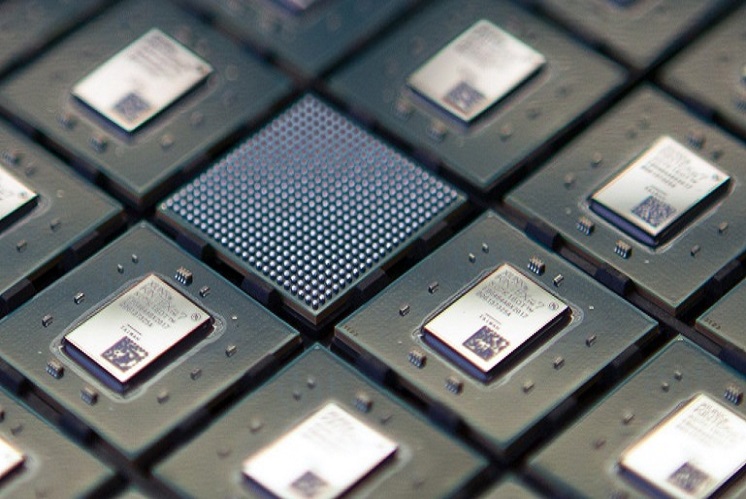
La implementación de chips complejos y de pequeño tamaño en los diseños de placas de circuito impreso es necesaria para adaptarse a los avances tecnológicos que se producen a nuestro alrededor. Estos circuitos integrados aumentan la densidad de E/S del embalaje. Por ello, los métodos de embalaje de alta densidad y bajo coste son muy necesarios. BGA es uno de ellos.
El ensamblaje de BGA es un proceso de montaje de matrices de rejillas de bolas (BGA) en una placa de circuito impreso mediante el proceso de reflujo de soldadura. Los BGA son componentes de montaje en superficie que utilizan matrices de bolas de soldadura para realizar interconexiones eléctricas. Estas bolas de soldadura se funden y establecen la interconexión cuando la placa pasa por el horno de reflujo de soldadura.
¿Cuáles son las ventajas de un ensamblaje BGA?
- Mejora el rendimiento eléctrico y térmico al tiempo que aprovecha el espacio.
- Reduce el grosor total del tablero.
- Minimiza las posibilidades de que se produzcan daños en la placa de circuito impreso, ya que los conductores BGA están fabricados con bolas de soldadura sólidas, lo que reduce los tiempos de mantenimiento y reparación.
- Adecuado para paquetes en miniatura con un elevado número de patillas.
- Ofrece una soldabilidad mejorada, lo que agiliza el proceso de montaje.
- Disipa el calor rápidamente gracias a su baja resistencia térmica.
Servicios de ensamblaje BGA (Ball Grid Array) con inspección por rayos X
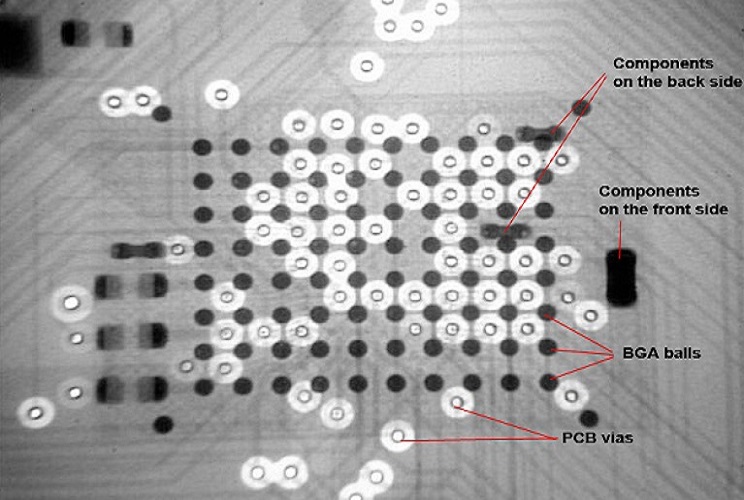
Hemeixin ha estado proporcionando el montaje BGA, incluyendo BGA Rework y BGA Reballing servicios en la industria de montaje de placas de circuito impreso desde 2003. Con equipos de colocación BGA de última generación, procesos de montaje BGA de alta precisión, equipos de inspección por rayos X de última generación y soluciones de montaje PCB completo altamente personalizables, puede confiar en nosotros para construir placas BGA de alta calidad y alto rendimiento.
Capacidad de montaje de BGA
Tenemos una gran experiencia en la manipulación de todo tipo de BGAs, incluyendo DSBGA y otros componentes complejos, desde micro BGAs (2mmX3mm) a BGAs de gran tamaño (45 mm); desde BGAs cerámicos a BGAs de plástico. Somos capaces de colocar BGAs con un paso mínimo de 0,4 mm en su placa de circuito impreso.
Proceso de montaje BGA/Perfiles térmicos
El perfil térmico es de suma importancia para BGA en el proceso de montaje de PCB. Nuestro equipo de producción llevará a cabo una cuidadosa comprobación DFM para revisar tanto sus archivos PCB como la hoja de datos BGA para desarrollar un perfil térmico optimizado para su proceso de montaje BGA. Tendremos en cuenta el tamaño del BGA y la composición del material de la bola BGA (con o sin plomo) para elaborar perfiles térmicos eficaces. Cuando el tamaño físico del BGA sea grande, optimizaremos el perfil térmico para localizar el calentamiento en el interior del BGA y así evitar huecos en las juntas y otros fallos comunes en el ensamblaje de PCB. Seguimos las directrices de gestión de calidad IPC Clase II o Clase III para asegurarnos de que los huecos sean inferiores al 25% del diámetro total de la bola de soldadura. Los BGA sin plomo se someterán a un perfil térmico especializado sin plomo para evitar los problemas de bolas abiertas que pueden derivarse de las bajas temperaturas; por otro lado, los BGA con plomo se someterán a un proceso especializado con plomo para evitar que las altas temperaturas provoquen cortocircuitos en las patillas. Cuando recibamos su pedido de montaje de PCB llave en mano, comprobaremos su diseño de PCB para revisar cualquier consideración específica de los componentes BGA durante nuestra meticulosa revisión DFM (diseño para la fabricación). La verificación completa incluye comprobaciones de la compatibilidad del material laminado de la placa de circuito impreso, los efectos del acabado superficial, el requisito de alabeo máximo y la holgura de la máscara de soldadura. Todos estos factores afectan a la calidad del ensamblaje BGA.
Soldadura BGA, retrabajo y reballing de BGA
Puede que sólo tenga unos pocos BGAs o piezas de paso fino en sus placas de circuito impreso que requieran el montaje de PCB para la creación de prototipos de I + D. Hemeixin puede ayudarle: ofrecemos un servicio especializado de soldadura de BGA para fines de prueba y evaluación como parte de nuestro enfoque en el montaje de prototipos de PCB. Además, podemos ayudarle con el retrabajo de BGA y el reballing de BGA a un precio asequible. Seguimos cinco pasos básicos para realizar el retrabajo de BGA: eliminación de componentes, preparación del lugar, aplicación de pasta de soldadura, sustitución de BGA y soldadura de reflujo. Garantizamos que el 100% de sus placas serán completamente funcionales cuando se las devolvamos.
Inspección por rayos X de ensamblajes BGA
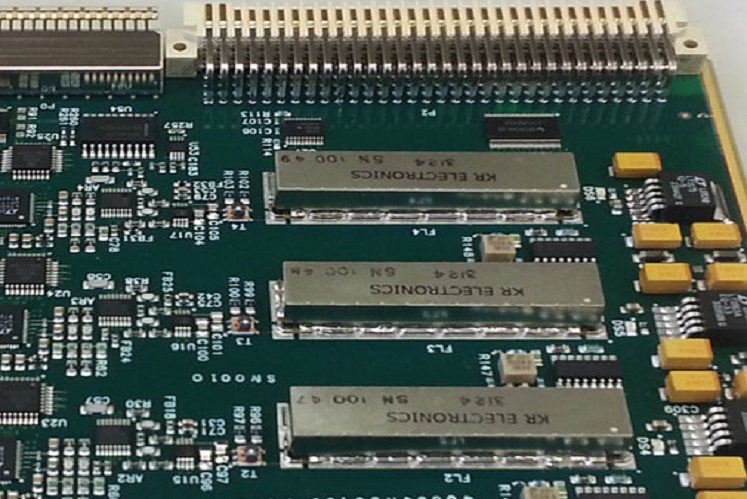
Utilizamos una máquina de rayos X para detectar diversos defectos que pueden producirse durante el montaje de BGA. Mediante la inspección por rayos X, podemos eliminar problemas de soldadura en la placa, como las bolas de soldadura y los puentes de pasta. Además, nuestro software de soporte de rayos X puede calcular el tamaño del hueco en la bola para asegurarse de que cumple las normas IPC Clase II o Clase III, según sus requisitos. Nuestros experimentados técnicos también pueden utilizar rayos X en 2D para generar imágenes en 3D con el fin de comprobar problemas tales como la rotura de las vías de la placa de circuito impreso, incluidas las vías en los diseños BGA y las vías ciegas/enterradas de las capas internas, así como las juntas de soldadura frías en las bolas BGA.
Si su requisito es el diseño de PCB BGA, PCB BGA, diseño de PCB BGA, montaje BGA o reelaboración BGA, puede estar seguro de que obtendrá una calidad y un rendimiento superiores, que a su vez repercutirán positivamente en el rendimiento de su producto final.
Montaje pasante
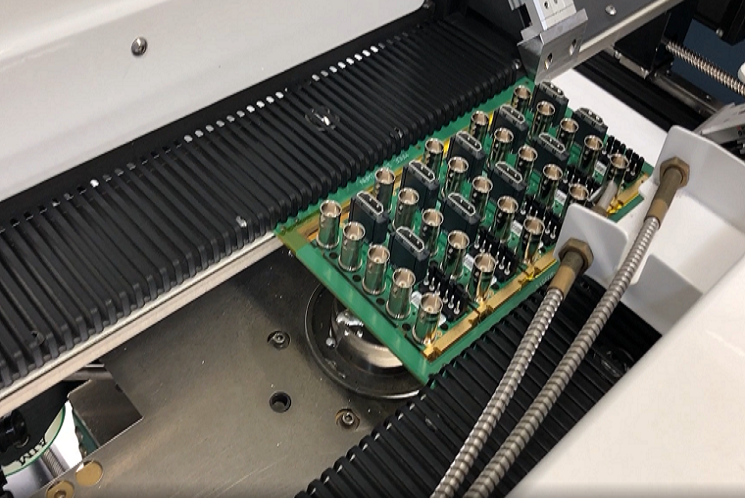
El montaje pasante es el proceso de montaje de componentes con plomo en una placa de circuito impreso que implica la perforación de orificios pasantes. Posteriormente, los componentes se sueldan a las almohadillas situadas en el lado opuesto de la placa, ya sea mediante soldadura manual o con una máquina de soldadura automática. La proporción de fundente de soldadura se establece cuidadosamente, ya que es esencial para mantener la calidad de la unión soldada entre la almohadilla y el cable del componente. Durante el proceso THA, los cables de los componentes se insertan desde la parte superior de la placa hasta la parte inferior a través de orificios perforados y, a continuación, se sueldan. Estos taladros pueden ser pasantes (PTH) o no pasantes (NPTH). Los fabricantes y diseñadores de placas de circuito impreso deben atenerse a las normas IPC 610 A y J-STD-001 para el montaje a través de orificios.
Montaje automatizado de placas de circuito impreso con taladros pasantes
¿Por qué ensamblar sus placas de circuito impreso con tecnología de taladro pasante manual cuando puede contar con una empresa de ensamblaje de placas de circuito impreso con taladro pasante que automatice y agilice el proceso? Cada vez son más las industrias que utilizan tecnología automatizada en sus procesos de fabricación. El ensamblaje automatizado de placas de circuito impreso con taladros pasantes permite a las máquinas colocar y soldar componentes de PCB más rápido de lo que los empleados podrían hacerlo manualmente, razón por la cual la práctica de combinar el ensamblaje manual y mecánico se ha extendido tanto.
Disponemos de una gran variedad de máquinas que hacen que el montaje sea más rápido y eficaz. Automatizamos procesos utilizando equipos como la máquina de inserción axial Universal 6287A, la Hollis Future I SMT y la Ace KISS-103. Trabajamos constantemente para integrar nuevas formas de maximizar la seguridad, la productividad y la eficacia en nuestra empresa para poder ofrecerle componentes de equipos de alta calidad.
Además de nuestras máquinas, disponemos de más de 50 estaciones de trabajo individuales con protección ESD para maximizar la seguridad. Utilizamos tanto la tecnología como las manos humanas para ayudar a garantizar que el proceso de soldadura se desarrolle sin problemas y que las placas de circuito impreso que desarrollamos y sus componentes creen una unión fuerte y duradera.
El ensamblaje de agujeros pasantes parcialmente automatizado ahorra tiempo y dinero, al tiempo que reduce el riesgo de errores en la producción. Esto conlleva el uso de equipos y maquinaria más fiables en las industrias a nivel mundial, lo que repercute positivamente en la seguridad y la eficacia. Como resultado, la automatización ha cambiado fundamentalmente la fabricación de placas de circuito impreso y seguirá influyendo en ella en los próximos años.
Comprobación de placas de circuito impreso con taladro pasante
Una gran parte de la fabricación y el montaje de placas de circuito impreso implica el proceso de comprobación de los productos una vez terminados. Estar a la altura de las expectativas de calidad es importante para nuestra empresa, por lo que hemos implementado un método de prueba e inspección minucioso y preciso en nuestras operaciones comerciales.
Ensamblar componentes eléctricos y entregarlos a los clientes sin someterlos antes a una inspección minuciosa deja margen para el error y aumenta el riesgo de averías en los equipos, lo que ralentiza las operaciones de las empresas. Nuestro sistema automatizado de pruebas e inspección detecta los defectos antes de que las placas de circuito impreso salgan por la puerta y evita este tipo de problemas.
En Hemeixin, utilizamos un sistema de inspección óptica 2 Mirtec MV-3L que busca problemas mecánicos y de fabricación en las nuevas placas de circuito impreso.
Utilizando todas estas herramientas, podemos detectar con precisión muchos tipos de defectos en el diseño y la construcción de la placa de circuito impreso ensamblada por taladro pasante, como daños o grietas, colocación inexacta de componentes, polaridad incorrecta y otros posibles problemas. Sólo permitimos que nuestros clientes adquieran nuestros servicios de PCB ensamblado por taladro pasante después de haber completado el proceso de inspección.
Con los servicios de montaje de placas de circuito impreso pasantes de Hemeixin, puede centrarse en otros elementos de su industria o empresa confiando en nosotros para construir y probar componentes eléctricos críticos para sus equipos. Nuestro exhaustivo proceso de pruebas protege sus inversiones y ayuda a garantizar que las placas de circuito impreso que ofrecemos actuarán como soluciones a largo plazo para su industria.
Montaje de placas de circuito impreso de tecnología mixta
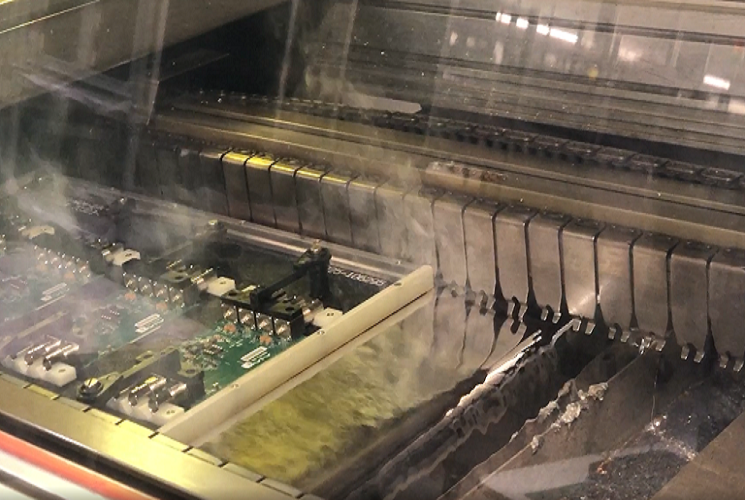
El ensamblaje de placas de circuito impreso de tecnología mixta tiene las propiedades tanto de la tecnología de montaje superficial (SMT) como de la tecnología de agujeros pasantes, de ahí su nombre. Por lo tanto, estos ensamblajes se utilizan con mayor frecuencia en las aplicaciones que requieren la combinación de ensamblajes de agujeros pasantes y SMT. Este tipo de montaje de PCB no utiliza pasta de soldadura. Hemeixin es uno de los fabricantes más experimentados y fiables de estos conjuntos en China. Tenemos capacidad para fabricar placas de circuito impreso con tecnología de una cara, doble cara y multicapa mixta.
Capacidad de montaje de placas de circuito impreso de tecnología mixta
Empleamos líneas de montaje automatizadas independientes de tecnología mixta para placas de circuito impreso. Esto nos permite ofrecer montajes completos de placas de circuito impreso y prototipos en plazos de entrega cortos. Nuestros clientes pueden beneficiarse de nuestras siguientes capacidades:
- Equipos de montaje automatizados de última generación
- Puntería láser y dosificación de flujo automatizadas
- Producción rápida de conjuntos de tecnología mixta densamente poblados
- Máquinas de colocación rápida de componentes de chip ultrapequeños y ultrafinos
- Limpieza acuosa automatizada en varias fases de producción
- Máquinas de ola y soldadura
- Cableado y montaje del chasis
Ensayos e inspección de ensamblajes de PCB de tecnología mixta
Seguimos rigurosos procedimientos de prueba e inspección, que nos permiten garantizar una alta precisión de las placas de circuitos:
-
Inspección óptica automatizada:
Nuestro equipo AOI proporciona una cobertura completa de fallos. Nos ayuda a inspeccionar a fondo los componentes en cuanto a su colocación óptica, orientación, valor, diferencias de color, cortocircuitos, juntas secas, etc. Es la forma más eficaz de inspeccionar todas las placas de circuito impreso de tecnología mixta, así como los ensamblajes SMT, Through-Hole y BGA.
-
Pruebas de rayos X:
Empleamos un sistema automatizado de rayos X de última generación para garantizar la máxima calidad en la inspección de placas de circuito impreso. Este tipo de pruebas nos ayuda a inspeccionar la calidad de los componentes de las placas de circuito impreso y cualquier fallo oculto que de otro modo sería invisible durante la inspección visual. Este tipo de prueba nos ayuda a eliminar cualquier defecto de fabricación en las etapas preliminares, y evitar diversos problemas de rendimiento costosos en el largo plazo.
-
Pruebas funcionales:
Esto se realiza para garantizar el correcto funcionamiento del montaje de PCB. El ensamblaje de PCB de tecnología mixta funciona mejor para aplicaciones que exigen componentes de montaje superficial y pasantes. En Hemeixin, ofrecemos una gama completa de opciones de proceso y montaje, incluido el montaje en placas de circuito con una cara, doble cara, flex y flex rígido, así como tecnología mixta multicapa.
Montaje sin plomo

La demanda de PCB sin plomo va en aumento para diversas aplicaciones industriales. Hay varias razones para la inmensa popularidad de este PCB, incluyendo cero emisiones de plomo al medio ambiente junto con la disminución de Inventario de emisiones tóxicas (TRI). Teniendo en cuenta los beneficios que aportan estos PCB, en Hemeixin producimos PCB sin plomo utilizando componentes y acabados de placa específicos libres de tóxicos. De este modo, cumpliendo con las directivas RoHS, también contribuimos a reducir los residuos electrónicos y trabajamos por la sostenibilidad medioambiental. Nuestros servicios de montaje de PCB sin plomo se ofrecen a aquellos clientes preocupados por el medio ambiente y su protección.
Nuestros servicios de ensamblaje sin plomo incluyen:
- Análisis de materiales sin plomo
- Montaje de placas sin plomo SMT y PTH
- Circuitos rígidos o flexibles sin plomo
- Soldadura selectiva sin plomo
- Soldadura por ola sin plomo
- Reparación de circuitos impresos sin plomo
- Encapsulado y revestimiento conformado sin plomo
- Evaluación del flujo de soldadura por ola y de los componentes
El proceso de montaje SMT sin plomo
El proceso de montaje de placas de circuito impreso RoHS exige que no se utilice ninguno de los materiales peligrosos enumerados en la Directiva RoHS en las placas, componentes o soldaduras. Las placas de circuito impreso desnudas utilizadas en el típico "proceso con plomo" suelen estar recubiertas con un acabado de plomo-estaño, por lo que el acabado de la placa debe modificarse significativamente para cumplir las normas RoHS y de ausencia de plomo.
El proceso de prototipos sin plomo también requiere que las placas se ensamblen a temperaturas más elevadas, normalmente de 30-50 grados o más. La temperatura más alta puede requerir que el sustrato de la propia placa de circuito y varios componentes se modifiquen para soportar las temperaturas más altas en el horno. Además, el nivel de sensibilidad a la humedad de los circuitos integrados, que indica cuánto tiempo puede estar expuesta la placa al aire, es aproximadamente 2 clases superior en el caso de las placas sin plomo. La vida útil de los materiales utilizados en las placas sin plomo también puede ser más corta.
Perfil
Para garantizar un perfilado adecuado de la temperatura de reflujo del horno, solicitamos una placa de circuito impreso sin plomo adicional junto con un juego extra de cualquier pieza crítica desde el punto de vista de la temperatura, es decir, BGA, piezas de calor, etc. Pueden ser piezas reales, piezas reales no funcionales o piezas falsas térmicamente equivalentes. La mayoría de los fabricantes de componentes grandes y caros pueden suministrar "muestras mecánicas" no funcionales específicamente para este fin. Además, proveedores como Practical Components proporcionan piezas térmicamente equivalentes específicamente para este fin.
Inspección
Debido a la composición metálica de la soldadura sin plomo, el aspecto visual puede diferir significativamente del de una unión de soldadura con plomo estándar. Con frecuencia, un primer vistazo dará la impresión de una unión soldada fría. Nuestro personal de inspección está formado conforme a las normas IPC-610D para garantizar que las juntas de soldadura sean sólidas y de alta calidad.
Desde el perfilado de la temperatura, la selección del acabado de la placa y el análisis de los componentes, la plantilla de la placa y la aplicación de pasta de soldadura, hasta la colocación de los componentes, las pruebas y el embalaje, garantizamos el cumplimiento de las normas de montaje de PCB sin plomo y RoHS. Esta estricta garantía de calidad nos ha hecho ganar una amplia ventaja competitiva y una enorme base de clientes de sectores como el de defensa, militar, naval y electrónico, entre muchos otros.
La entrega puntual de productos de calidad ha sido nuestro lema desde nuestros inicios. Lo mismo puede decirse de nuestros servicios de montaje de PCB sin plomo. Contamos con la técnica, la excelencia en la fabricación y el personal adecuado para producir PCB sin plomo estándar y personalizados que superen las expectativas del cliente. Ya se trate de un prototipo o de una producción a pequeña o gran escala, en Hemeixin estamos equipados para afrontar los retos. Además, con un equipo de personal altamente cualificado, garantizamos el cumplimiento de las especificaciones técnicas dadas por los clientes como en el montaje final.
Montaje de PCB de bajo volumen
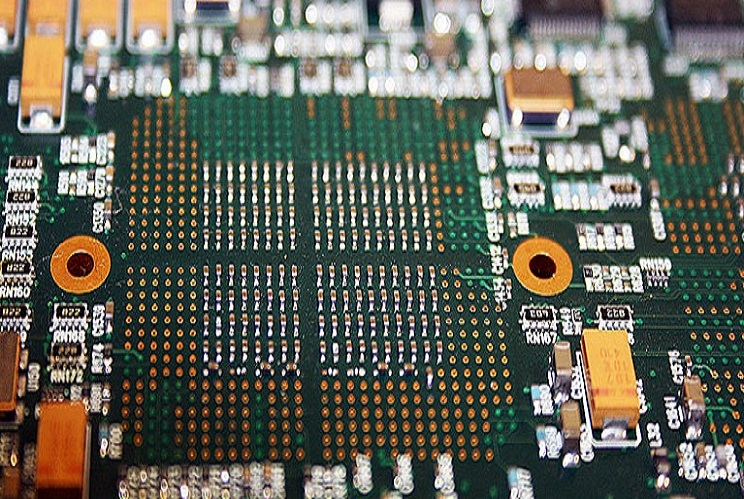
Bajo volumen, como el término indica, es un lote con un número limitado de lotes de montaje. Mientras que algunos OEM que fabrican productos electromecánicos necesitan PCBA a granel, un montaje de PCB de bajo volumen puede ser necesario para un producto de edición limitada o con requisitos muy específicos. En estos casos, es fundamental realizar primero un prototipo de montaje de PCB de bajo volumen, ya que nos dará una idea del producto final y de si requiere algún cambio. Hemeixin es un experimentado fabricante por contrato de servicios completos de electrónica; sin embargo, el volumen nunca ha sido un problema para nosotros. Ofrecemos servicios de ensamblaje de PCB incluyendo la creación de prototipos incluso para pedidos de bajo volumen e independientemente de la complejidad del requisito.
Capacidad de montaje de PCB de bajo volumen
- Nuestras instalaciones de última generación con herramientas y máquinas avanzadas, equipos experimentados y un presupuesto que puede atender montajes de prototipos de bajo volumen nos permiten conseguir PCB de bajo volumen con las especificaciones requeridas. Por presupuesto entendemos que podemos necesitar utillaje sólo para una pequeña cantidad de placas o simplemente un prototipo; sin embargo, merece la pena el coste y el esfuerzo, ya que sirve de referencia futura para los montajes de PCB de muchos fabricantes de equipos originales.
- Disponemos de estrictos procedimientos de prueba e inspección. Las técnicas de prueba incluyen la inspección óptica automatizada (AOI), la inspección microscópica, la inspección por rayos X, la prueba de sonda volante (FPT) y la inspección visual.
- Ofrecemos placas de una o dos caras, en su mayoría flexibles o rígidas-flexibles, para nuestros montajes de PCB de bajo volumen, que pueden constar de apenas 200-250 placas o menos.
- Para nuestros prototipos de bajo volumen y montaje de placas de circuito impreso, utilizamos diferentes técnicas de montaje de componentes, como la tecnología de montaje superficial (SMT) y la tecnología de agujero pasante chapado (PTH). Además, ofrecemos matrices de rejilla de bolas (BGA), uBGA/Micro BGA, embalaje a escala de chip (CSP), etc.
- Utilizamos soldaduras con plomo y conformes con la directiva RoHS, así como técnicas de soldadura avanzadas, como la soldadura por ola selectiva, la soldadura pb88, la soldadura de alto punto de fusión (hmp) y la soldadura au80.
- Aceptamos diseños de PCB en formatos de archivo Gerber RS-274X, 274D, Eagle y DXF y DWG de AutoCAD. Puede compartirlos junto con su lista de materiales (BoM).
En Hemeixin, comprendemos estas dificultades y nos hemos propuesto elevar el listón de nuestros servicios de montaje de PCB de bajo volumen para diferenciarnos de la competencia. Nos complace ofrecer los más altos niveles de calidad que cabría esperar de una instalación de ensamblaje de placas de circuito impreso de primer nivel, conservando al mismo tiempo la flexibilidad de un fabricante de bajo volumen.
Servicios de montaje de PCB en kit
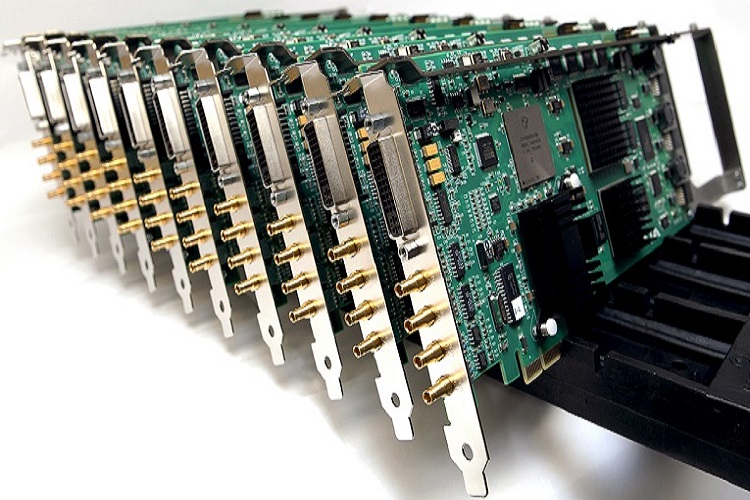
Kitting es el proceso de reunir un conjunto de componentes como un kit necesario para montar placas de circuitos. En este caso, el cliente proporciona todos los componentes que van en la placa. El kitting reúne todos los materiales/piezas en un único paquete. Es extremadamente beneficioso para el inicio del montaje, ya que todos los componentes necesarios están disponibles, verificados y colocados en el embalaje adecuado.
El diseño de cada placa y los requisitos de cantidad varían en función del cliente. Por tanto, los criterios de los kits para cada proyecto de montaje son diferentes. A pesar de ello, hay reglas particulares que tener en cuenta y normas que seguir. La analogía podría ser la de cocinar una receta cuando todos los ingredientes se recogen del mercado o de la cocina y la despensa. Todos estos ingredientes se reúnen en la mesa de la cocina y luego se cocinan.
En este tipo de montaje, el cliente suministra todos los componentes al fabricante para su ensamblaje. Los componentes a suministrar incluyen placas de circuito impreso desnudas, componentes electrónicos y todos los archivos de diseño de PCB necesarios, y el fabricante ensamblará los componentes utilizando equipos automatizados. Este tipo de montaje de PCB también se denomina montaje de PCB en consignación. Ha habido una creciente demanda de servicios de montaje de PCB en kit, debido a las siguientes razones:
- Es una de las formas más económicas de fabricar placas de circuito impreso.
- El cliente puede estar seguro de que se utilizan componentes y placas de circuito impreso suministrados por ellos y de que no se utilizan piezas de calidad inferior en el proceso.
- El cliente controla mejor el coste de producción.
En resumen, el montaje en kit ayuda a los fabricantes de equipos originales a evitar problemas relacionados con la calidad y a mejorar su capacidad de comercialización.
Aspectos destacados de los servicios de montaje de PCB en kit de Hemeixin
En Hemeixin, ofrecemos asistencia en la lista de materiales si es necesario, de lo contrario, simplemente aceptamos su lista. La lista de materiales (BoM) es un aspecto muy importante de un conjunto de PCB kitted ya que tiene la lista de materiales, cantidades, cantidad mínima de pedido, precios, números de pieza, tiempo estimado de finalización, y mucho más. Después de que nos proporcione los detalles, analizamos los detalles como la viabilidad, la compatibilidad con los requisitos de su aplicación, la calidad de los componentes, etcétera. Podemos ofrecerle fácilmente un presupuesto basado en sus requisitos de montaje de PCB en kit. Ofrecemos las siguientes características como parte de nuestros servicios de montaje de PCB en kit
Tipos de montaje de PCB: Ofrecemos los siguientes tipos de montaje de PCB en kit.
- Montaje en superficie (SMT)
- Orificio pasante
- Tecnología mixta (SMT/agujero pasante)
- SMT/PTH de una y dos caras
- Piezas grandes en ambos lados
- BGA en ambos lados
- También apoyamos proyectos de introducción de nuevos productos (NPI).
Pruebas de PCBA: Llevamos a cabo pruebas internas utilizando métodos manuales y automatizados en cada etapa del montaje de PCB. Esto incluye pruebas funcionales, así como el montaje de componentes, el diseño físico, etcétera. Nuestras instalaciones en China están equipadas para ello.
Si es usted un OEM de dispositivos eléctricos, electrónicos o electromecánicos y necesita asistencia en materia de montaje de placas de circuito impreso en kit, puede confiar plenamente en nosotros. Somos expertos en ofrecer servicios de montaje de PCB en kit.
Proceso de montaje de PCB
El proceso de montaje de PCB tiene lugar después de la fabricación de PCB, donde la estructura de la placa se forma completamente de acuerdo con los requisitos del cliente. El montaje de PCB abarca acciones que van desde la preparación de la plantilla y la impresión de pasta de soldadura hasta la colocación de piezas SMD, la formación de enlaces en el horno de curado y la inspección final de la funcionalidad de la PCB. Tras la preparación del esténcil, tiene lugar la impresión de la pasta de soldadura. En esta fase, las diminutas aberturas que presentan los puntos de montaje de los componentes eléctricos deben rellenarse con una precisión excepcional. De lo contrario, pueden producirse problemas graves, como la formación de puentes. Los puentes suelen tener un tamaño micro y no son visibles a simple vista. Eso hace que sean difícilmente detectables si no se utilizan dispositivos de inspección de última generación. Aún así, son el problema más común en el proceso de ensamblaje de placas de circuito impreso, y provocan cortocircuitos o incluso la quema de componentes. Por ello, en Hemeixin utilizamos la última tecnología de impresión de pasta de soldadura, garantizando que cada placa de circuito impreso funcione correctamente al final de la línea de montaje.
Otra parte fundamental del proceso de montaje de placas de circuito impreso es el posicionamiento de los componentes electrónicos mediante la máquina pick and place. Las líneas conductoras de la placa son muy pequeñas y deben alinearse con las partes conductoras de los componentes electrónicos. Por tanto, los dispositivos electrónicos deben orientarse y colocarse en la placa con la máxima precisión. Utilizamos los sistemas ópticos de tres puntos fiduciales más precisos para colocar los dispositivos de montaje en superficie. Por último, al final de la línea de montaje de PCB, la conexión firme y estable entre los SMD y la placa se consigue en el horno de curado. La soldadura en pasta permite la longevidad y durabilidad de las placas de circuito impreso, que son nuestros objetivos finales además de la máxima calidad de las placas de circuito impreso.